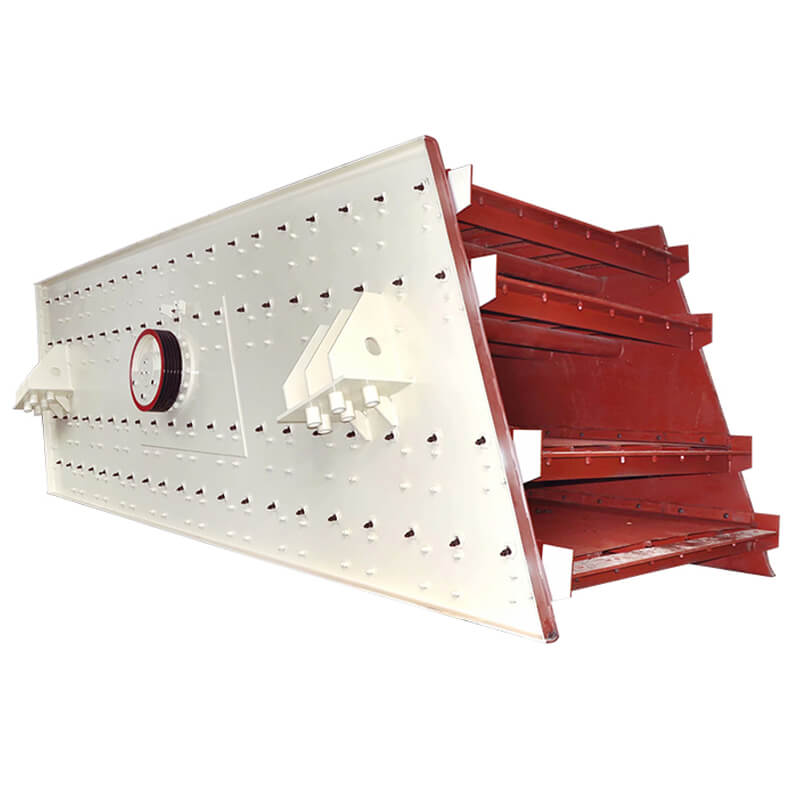
High Frequency Vibrating Screen
Capacity: 10-500tph
Motor Power: 2.2kW-30kW
Screen Layer: 1-4 available
Screen Materials: Steel, ethoxylate resin
Applications: Mining, quarrying, and so on industries to screen ore, sand, and gravel effectively.
High Frequency Vibrating Screen Overview
A vibrating screen is a kind of mine classification machine for ore, mine, sand, gravel, coal, slurry, etc. which consists of a screen and a vibrator. Generally below 50 mesh for the coarse screen, and 80 mesh for the fine screen. The vibrator is an eccentric wheel that rotates under the drive of the motor, making the sieve frame vibrate. Because of the vibration of the sieve frame, the thicker solid particles are left on the sieve surface when they flow to the sieve surface and are discharged from one end along the sloping surface. The finer solid particles and the mud liquid flow through the sieve hole to the mud pond together.
Vibrating Screen Types
The vibrating sieve can be divided into the mining vibrating screen, light fine vibrating screen, experimental vibrating screen, also can be divided into the linear vibrating screen, circular vibrating screen, high frequency vibrating screen, double deck vibrating screen, single deck vibrating screen, and so on.
The vibration screen is widely used in coal and other industries as a material classification, mineral washing, dehydration, and sand screening machine. It is commonly used in mining, coal, smelting, building materials, refractory, light industry, and chemical industries for its high production efficiency, good classification effect, and convenient maintenance.
Advantages
Application advantages of high frequency screen in mineral processing
- For iron ore, limonite: Uses the high frequency vibration fine screen to use in the ore concentrate graduation, by the screen-out low-grate large grain continually living body, is same when the ore mill handing ability, but stably enhances the ore concentrate personal status 1%-3%,And reduced the utility over-grinding. Under the same ore concentrate personal status premise, the ore concentrate average granularity increases thickly, but causes the ore concentrate to filter the condition improvement, may cause to filter the cake moisture content to reduce 0.5%-1%.
- For tungsten, tin, tantalum, niobium, finely quarry: Uses the high frequency vibration fine screen to replace the spiral sorting machine, the cyclone graduation, or with spiral sorting machine, cyclone combination graduation, with grinding machine close up, but remarkably reduces the great density utility smashing, has enhanced the dressing efficiency, the returns-ratio may enhance 10%-15%.
- For quartz sand, long quarry: Uses in the stick rubbing-the screening flow, but stably produces the certified product.
- For the metal power system takes: Produce -38mu m between -351μm(400item to 40 item)the metal powder.
Structures & Working Principle
Vibrator Screen Structure
The main parts of a vibrating screen are the mainframe, screen, electric vibrators, electric motor, rub spring, and coupler.
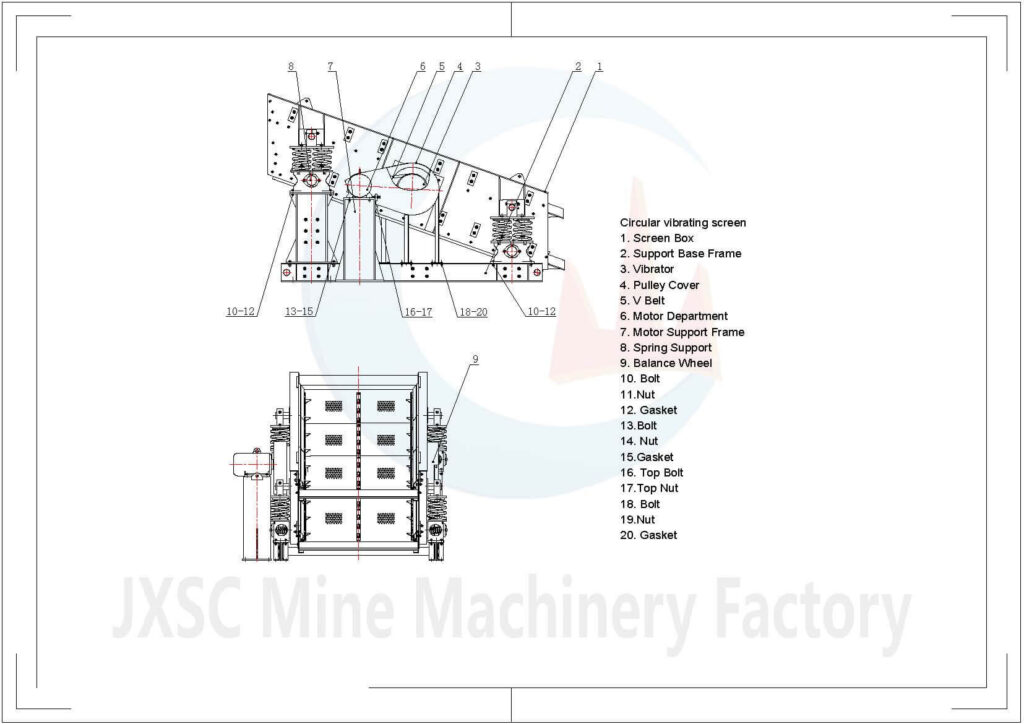
Vibrating Screen Machine Working Principle
Vibrating screen uses electric exciter as a vibrating source, the material will be thrown around the screen, at the same time doing forward sports, in order to achieve the screening purpose. Material from the feeder evenly enters into the machine’s feeding inlet, with multilayer sieves to produce various products and unqualified products on the screen or under the screen, then discharging from the outlet respectively. It can be used in the automatic production line.
In the working process, the dynamic performance of the vibrating screen directly affects the screening efficiency and service life. The vibrating screen uses the vibration excited by the vibrating motor as the vibration source so that the material is thrown up on the screen Mesh and moves forward in a straight line Through the multi-layer screen to produce a number of the screen on the screen, screen under the material, respectively from their respective export discharge.
Technical Parameters
Model | JXSC-1036 | JXSC-1236 | JXSC-1536 | JXSC-1545 | JXSC-1836 | JXSC-1845 | JXSC-2045 | JXSC-2460 |
Capacity (t/h) | 10-15 | 18-65 | 30-90 | 30-90 | 40-120 | 40-120 | 60-160 | 80-250 |
Screening Surface Size (mm) | 1000*3600 | 1200*3600 | 1500*3600 | 1500*4500 | 1800*3600 | 1800*4500 | 2000*4500 | 2400*6000 |
Sieve Size (mm) | Customized according to customer requirements | |||||||
Double Amplitude (mm) | 0-5 | 0-5 | 0-5 | 0-5 | 0-5 | 0-5 | 0-5 | 0-5 |
Power (kW) | 2*1.1 | 2*2.2 | 2*3.7 | 2*5.5 | 2*5.5 | 2*7.5 | 2*11 | 2*15 |
Voltage (v) | 380 | 380 | 380 | 380 | 380 | 380 | 380 | 380 |