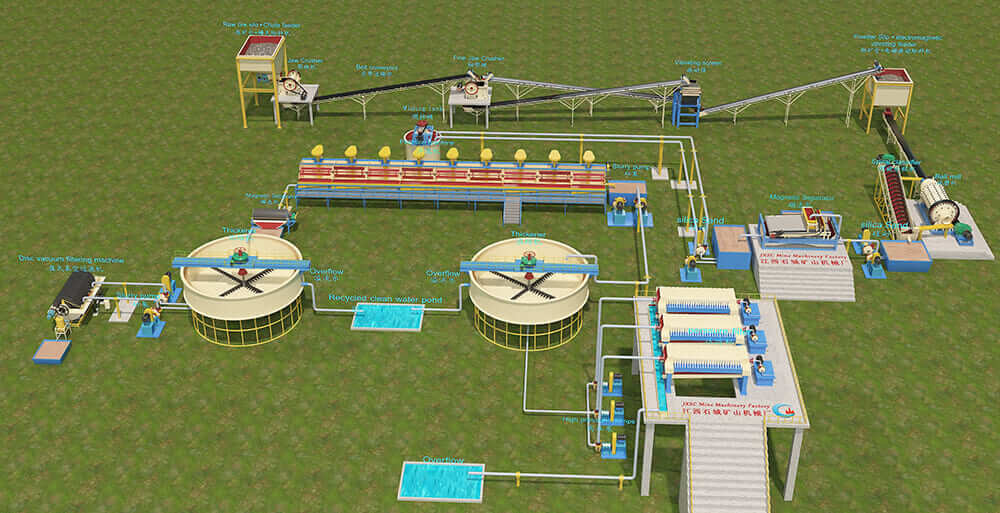
Feldspar Mining Process
The main harmful mineral present in feldspar ore is iron, and other impurity minerals include mica, quartz, clay, garnet, tourmaline, chlorite, and others. Depending on mineral properties, feldspar ore beneficiation methods are mainly magnetic separation, flotation, gravity separation, or combined processes.
Feldspar Mining Process
Introduction
About Feldspar Ore
Feldspar is an aluminosilicate mineral of alkali or alkaline earth metals such as potassium, sodium, calcium, and a small amount of barium. The proportion of Feldspar in the earth’s crust is as high as 60%, and it can appear in igneous rocks, metamorphic rocks, and sedimentary rocks. Feldspar is the main mineral component of almost all igneous rocks and is significant for classifying rocks. In industrial applications, Feldspar is mostly used as a flux for ceramics, glass, and other materials.
Feldspar Types: There are many kinds of feldspar, such as albite, anorthite, barium feldspar, barium feldspar, microclinic feldspar, orthoclase, feldspar, etc.
Feldspar Color: They all have a glassy sheen and come in various colors. There are colorless, white, yellow, pink, green, gray, black, etc. Some are transparent; some are translucent. Feldspar itself should be colorless and transparent. The reason why it is colored or not completely transparent is because it contains other impurities.
Feldspar Shape: Some are block-shaped, some are plate-shaped, some are columnar or needle-shaped, etc.
Feldspar Application: Feldspar, which is rich in potassium or sodium, is mainly used in the ceramic, glass, and enamel industries. Feldspar, which contains rare elements such as rubidium and cesium, can be used as a raw mineral material to extract these elements. With beautiful colors, Feldspar can be used as a decorative stone and secondary gemstone.
Mineral Processing
Feldspar Ore Processing
Feldspar Crushing
The feldspar ore is crushed at the processing plant to reduce it to a size suitable for further processing. The crushing stage helps in liberating the feldspar minerals from the surrounding rock.
Feldspar Grinding
The crushed ore undergoes grinding to reduce the particle size further. This step is crucial for separating feldspar from other minerals and impurities.
Feldspar Washing & Desliming
The purpose of the ore washing operation is mainly to remove clay, fine mud, mica, and other impurities in the potash feldspar, reduce iron oxide content in the potassium feldspar, and increase the potassium and sodium content. This step is mainly for potassium feldspar ore of weathered granite or feldspathic placer, using a vibrating screen or washing tank to separate impurities from coarse-grained feldspar under the action of water flow. The desliming operation aims to remove the primary slime in the potassium feldspar ore and the secondary slime produced by grinding through desliming buckets, hydrocyclones, and other equipment. These slimes will affect subsequent flotation, magnetic separation, and other separations. Especially for flotation operations using amine collectors, these sludges will reduce the separation effect and consume many collectors.
Feldspar Separation
Various methods, such as gravity separation, magnetic separation, and flotation, are employed to separate feldspar minerals from other minerals and impurities. These processes are designed to concentrate and purify the feldspar.
Feldspar Drying
After separation, the feldspar concentrate may be dried to reduce moisture content, making it suitable for various industrial applications.
Feldspar Process Plant
10 TPH Feldspar Process Plant
Used Equipment: Raw material hopper, chute feeder, rough jaw crusher, belt conveyor, fine jaw crusher, vibrating screen, fine ore bin, electromagnetic vibrating feeder, ball mill, spiral classifier, magnetic separator, slurry pump, flotation machine, thickener, filter machine.
Raw Ore: Raw feldspar ore contains iron, calcium, mica, and other impurities, so the feldspar ore dressing process includes magnetic separation, flotation, or gravity separation to remove iron, mica, and other impurities to obtain high-grade feldspar.
The beneficiation process in detail:
1- Crushing section
Utilize rough jaw crusher, fine jaw crusher, and vibrating screen to form a closed crushing circuit to make 200mm rock ore down to 20mm. Thus, it ensures the particle size of the material entering the grinding section is qualified.
2- Grinding section
Utilize ball mill and spiral classifier to form a closed grinding circuit to achieve more than 90% discharging size 200mesh(0.074mm). Thus, it ensures the particle size of the material entering the flotation section is qualified.
3- Magnetic separation section
Use a two-stage low-intensity and high-intensity magnetic separation process to remove magnetic minerals in feldspar ore to the maximum extent. Low-intensity magnetic separation can remove magnetite(Fe3O4), and high-intensity magnetic separation can remove hematite, limonite, ilmenite(Fe2O3)
4- Flotation section
The flotation process is used to remove impurities in the feldspar ore further to obtain high-grade feldspar concentrate.
5- Dewatering process for concentrate
The dewatering process for the concentrate utilizes a thickener and disc vacuum filter machine. Use a slurry pump to send concentrate to the thickener; the overflow of the thickener goes to a clear water pond, and the underflow goes to the disc filer machine for dehydration. After being dehydrated by a disc filter machine, the moisture concentration is less than 10%.
6- Tailing dry discharging process
All tailings are first pumped to the cone thickener to adjust the suitable concentration; the overflow of the cone thickener goes to the recycled clear water pond, and the underflow goes to the plate filter machine for dehydration. Finally, the moisture of the tailing is less than 10%; this is the tailing dry discharging process.