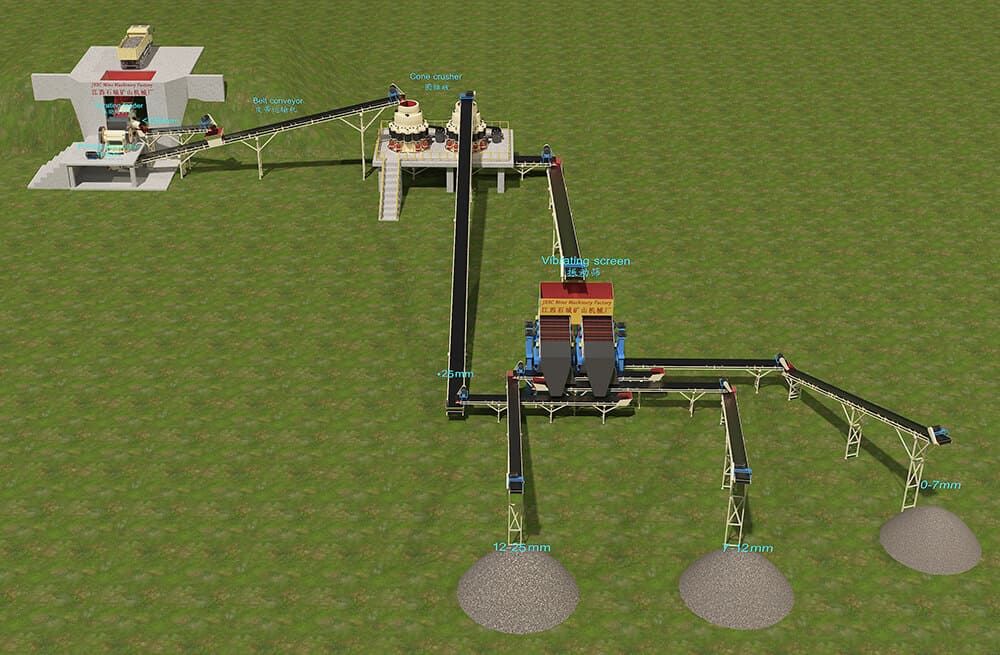
Granite Crushing Process
The granite crushing process involves three stages: coarse crushing -> medium fine crushing -> screening.
The granite sand-making process includes four stages: coarse crushing -> medium fine crushing -> sand making, -> screening.
Granite Crushing & Sand Making Process
Introduction
About Granite
Granite is a type of igneous rock that forms from the slow crystallization of magma beneath the Earth’s surface. It is composed mainly of quartz, feldspar, and mica, with varying amounts of other minerals. Because granite is a plutonic rock, it often forms well-developed mineral particles that can be discerned with the naked eye, hence its name. Granite is not easily weathered, has beautiful color, and can maintain its appearance for over a hundred years. Due to its high hardness and wear resistance, granite is used in building decoration projects, hall floors, and as a high-quality material for open-air carvings.
Advantages: High hardness, wear resistance, corrosion resistance, oxidation resistance, etc.,
Uses: Usually used as decorative materials for highway construction.
Granite crushing equipment: Jaw crusher, cone crusher, impact crusher, etc.
Mineral Processing
Granite Crushing Processing
Granite Coarse Crushing
The raw granite ore is continuously and uniformly fed to the jaw crusher by the vibrating feeder through the silo. The jaw crusher crushes large pieces of granite to a specific particle size through repeated squeezing. , And then transported by the belt conveyor to the cone crusher for medium and fine crushing.
Granite Medium And Fine Crushing
The granite conveyed to the cone crusher is crushed to a small particle size under the laminated crushing principle and enters the next step.
Granite Screening And Classification
The finely crushed granite material is sent to the circular vibrating screen under the action of the belt conveyor. The circular vibrating screen divides it into materials with qualified particle size and materials with unqualified particle size, and materials with qualified particle size are sent to the finished material pile; the unqualified materials are re-transported to the cone crusher to continue the crushing process until all the material particle size meets the requirements.
There is a sand-making step between medium and fine crushing and screening for the granite sand-making process. In the sand-making process, the crushed materials are larger than the size of the two-layer screen mesh, and the stones are transported to the sand-making machine through a belt conveyor for fine crushing and shaping.
Granite Crushing Plant
400TPH Complete Granite Crushing Plant For Indonesian Customer
This setup is a 400tph complete granite crushing plant for an Indonesian customer.
Raw Ore: The max input size is 850mm, and output sizes are 0-7mm, 7-12mm, and 12-25mm.
Configured equipment as follows:
- A hopper
- vibrating feeder DN 6013
- primary jaw crusher PE-1000*1200
- 2 sets cone crusher DN 1626
- 2 sets vibrating screen 3YD2470
- 12 pcs belt conveyors
400tph granite crushing plant process:
1. The Excavator unloads the stones into the hopper, and the stone enters the vibrating feeder from the lower part of the hopper;
2. The vibrating feeder feeds the 130-850mm stones evenly to the primary jaw crusher; the vibrating feeder will have a gap of 130mm grizzly bar. The 0-130mm stone will fall into the 1st belt. And it will be transferred to the 2nd main belt. And they will be transported to the 1st coarse cone crusher.
3. The first coarse cone crusher is for crushing the output from the jaw crusher. The second fine-crushing crusher is for crushing the oversized +25mm stone from the two vibrating screens. The 3rd conveyor is under the two cone crushers. The 3rd conveyor sand will flow to the 4th conveyor, carrying the crushed stones to the aerial hopper.
4. The aerial hopper will feed two sets of vibrating screen 3YD247zero with 7mm, 12mm, and 25mm mesh. The +25mm will be sent back to the fine cone crusher to be crushed again.
5. After the screening, three outputs will be 0-7mm, 7-12mm, and 12-25mm. Each output will need two separate conveyor belts. One is under the two vibrating screens, the other for undertaking it.