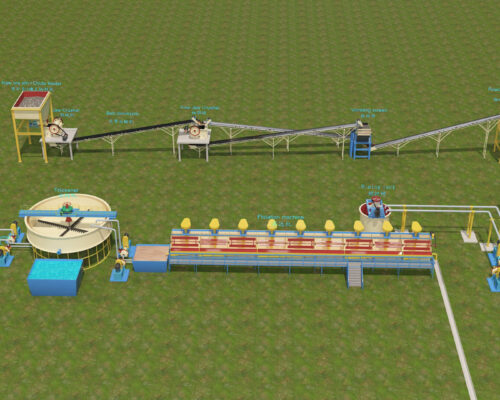
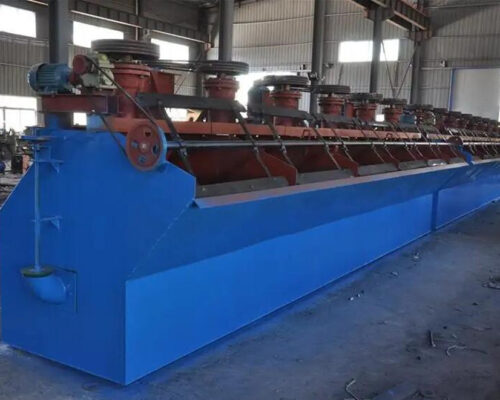
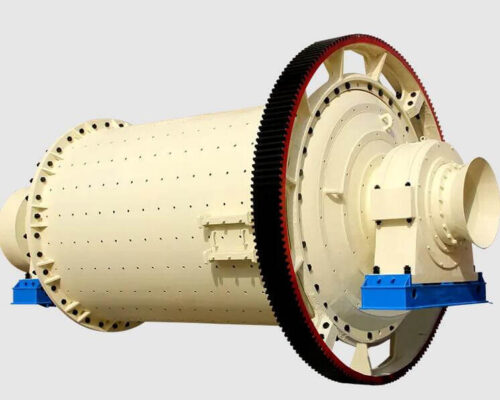
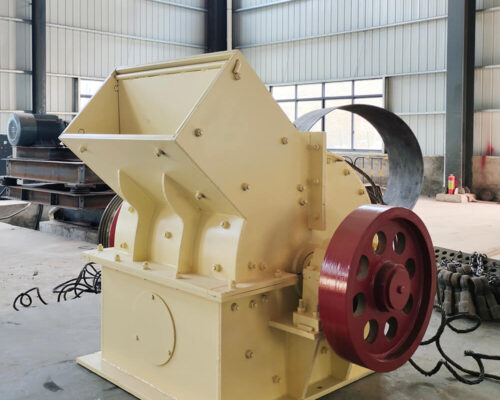
Graphite Ore Mining Process
The graphite ore mining process is mainly suitable for all kinds of graphite with different crystal habits and graphite accompanied by mica, silicate minerals, or pyrite. The beneficiation process includes flotation, electrostatic separation, gravity separation, etc. And flotation is the most widely used process.
Graphite Mining Process
Introduction
About Graphite
Graphite is a metamorphic carbonaceous matter of organic origin, most commonly found in marble, schist, or gneiss. Coal seams can partially form graphite through thermal metamorphism, and a small amount of graphite is the primary mineral of igneous rocks. Graphite is a mineral of extremes. It is extremely soft, cleaves with very light pressure, and has very low specific gravity. Due to its unique structure, it has many characteristics, such as high-temperature resistance, thermal shock resistance, electrical conductivity, lubricity, chemical stability, and plasticity. It has always been an indispensable and important strategic resource in the military industry, modern industry, and high-tech development.
Mineral Processing
Graphite Beneficiation Process
Graphite Flotation Separation
Graphite has good natural buoyancy and hydrophobic properties. Therefore, most processing plants use flotation to purify graphite ore, adding a series of flotation reagents to the gas-liquid interface to enrich the graphite ore on the gas-liquid interface, separating it from impurity minerals. A commonly used collector is coal tar. The foaming agent is mainly pine oil or butyl ether oil, and the corrosion inhibitor is mostly water glass and sodium fluorosilicate.
The flotation process of flake graphite ore mainly adopts multi-stage grinding, multiple separations, coarse concentrate regrinding, and separation process to protect the scales.
Graphite flotation beneficiation can make graphite grade reach 80%-90%, even close to 95%. And it finds that the method has the characteristics of low chemical consumption, low energy consumption, and low cost. However, for graphite ore containing extremely fine silicate minerals and elemental compounds such as potassium, calcium, sodium, magnesium, and aluminum, monomer dissociation cannot be achieved in the grinding stage, and it needs to be purified again by other processes after flotation.
Graphite Flotation Plant
This setup is the Sulfide Rock Minerals Processing plant, suitable for processing Sulfide rock Gold, Copper, Silver, Zinc, Lead, Fluorite ore, Graphite, etc. Has a high recovery ratio for sulfide-type minerals. Usually can reach about 85-90% depending on material conditions.
Graphite Gravity Separation
Graphite gravity separation accord the specific gravity difference between graphite ore and gangue to sort. The paragenetic minerals in graphite ore can divide into heavy, medium, and light minerals according to specific gravity. Among them, heavy minerals (specific gravity > 3.32) mainly include pyrite, pyrrhotite, limonite, zoisite, etc., followed by titanite, zircon, white titanium, monazite, and scheelite. Minerals with medium specific gravity (with a specific gravity between 2.9 and 3.32) mainly include diopside, tremolite, and occasionally apatite. Among the light minerals (specific gravity <2.9), there is a difference in the particular gravity of graphite and its associated minerals. Therefore, we can separate heavy minerals by gravity separation to obtain rough concentrate mainly composed of graphite.
Graphite Electric Separation
Electric separation is a physical separation method that utilizes the different electrical properties of various minerals and materials for separation. For graphite ore beneficiation, graphite ore has good conductivity, while gangue minerals such as feldspar, quartz, pyrite, etc., have poor conductivity.
The effective treatment particle size of the electric separation method is usually 0.1-2mm. However, the upper limit of processing particle size can reach 5mm for flake or low-density graphite ore. The processing particle size of the wet high-gradient electric separator can reduce to the micron level.
Graphite Beneficiation Process & Equipment
The graphite beneficiation process can generally divide into crushing, grinding, sorting, and middling processing operations. We should determine the specific beneficiation process according to the particular type of graphite.
The leading beneficiation equipment of graphite includes crushing equipment, grinding equipment, sorting equipment, dehydration equipment, and grading equipment. Since different processing stages will use various equipment, there are many combinations of graphite beneficiation equipment.
- Crushing stage: The coarsely crushing of crystalline and aphanitic graphite ore can use a jaw crusher.And medium and fine graphite crushing use cone crushers and hammer crushers.
- Grinding stage: graphite grinding equipment can choose a ball mill and rod mill.
- Sorting stage: It can use JJF and XCF flotation machines for flotation operation.
- Dehydration stage: It can use the diaphragm filter press, centrifugal dehydrator, and dryer to dehydrate graphite ore.
- Classification stage: It often uses high square sieves to classify grading graphite products and seldom uses planar vibrating screens and rotary sieves. Among them, the square sieve is a commonly used screening equipment for graphite product classification in mineral processing.