Iron Ore Processing
Iron ore is mainly used in the production of iron and steel. Natural iron ore needs to be processed through a series of processes such as crushing, grinding, magnetic separation, and flotation to gradually select iron.
Iron Ore Beneficiation
Introduction
About Iron Ore
Iron ore is a mineral aggregate containing iron elements or iron compounds that can be economically utilized. Any ore containing economically available iron is called iron ore.
There are many kinds of iron ores. The main 4 types of iron ores are Magnetite (Fe3O4), Hematite (Fe2O3), Limonite(Fe2O3.nH2O), and Siderite (FeCO3). According to the different properties of iron ores, their beneficiation methods are also different.
Mineral Processing
Iron Ore Dressing
The iron ore dressing process is aimed at the processing of iron ore materials, which is divided into crushing and screening, grinding and classification, separation, and dehydration. Crushing and screening refers to the crushing and screening of iron ore to ensure that the particle size of crushed ore can provide ore that meets the requirements of block size for the next process flow. Through the treatment of ball mill and classifier, the ore conforms to the requirements before mineral separation is obtained. Mineral separation generally includes gravity separation, flotation, and magnetic separation. Generally, iron ore can use the separation process according to the nature of iron. Dehydration is to concentrate, filter and dry the ore after mineral separation, and finally select the iron ore.
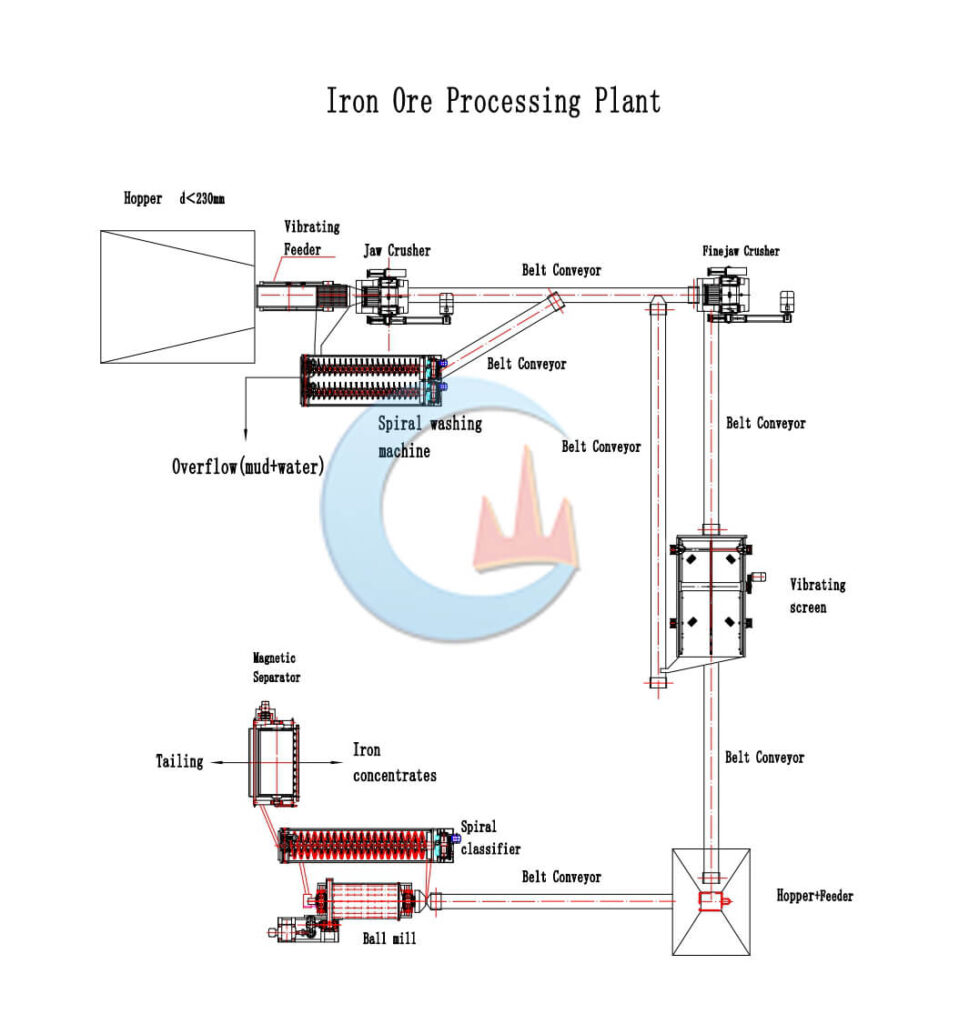
Due to differences in ore properties, different processes and equipment are used in iron ore dressing, but most iron ore processing processes need to go through the following stages.
The large iron ore is fed into the jaw crusher by the vibrating feeder through the silo for preliminary crushing. After reaching a certain particle size, it enters the next process. The coarsely crushed iron ore is screened by a circular vibrating screen and then conveyed by a belt conveyor to a cone crusher for secondary crushing. In order to improve the fineness of iron ore, the iron ore after secondary crushing enters the ball mill for grinding to meet certain fineness requirements. After that, the material will enter the magnetic separator. Since the gangue dropped from the upper magnetic roller also contains some ore particles with weak magnetic properties, these ore particles will enter the lower magnetic roller for magnetic separation. The finished iron ore particles will enter the secondary separation collection hopper and be collected as finished products. The thrown gangue will be discharged from the tailings mouth. So far, the magnetic separation stage is completed.
China’s concentrators generally adopt the three-stage crushing process of coarse crushing, medium crushing, and fine crushing to crush iron ore. 1.2m or 1.5m jaw crushers are mostly used for coarse breaking, cone crushers are used for medium breaking and fine breaking, 2.1m or 2.2m standard cone crushers are used for medium breaking, and 2.1m or 2.2m short head cone crushers are used for fine breaking. The ore that passes through coarse crushing has a block size of no more than 1m, then passes through medium and fine crushing, and is sieved into final products with ore particle size less than 12mm and sent to the grinding tank.
The limonite fine ore with particle size less than 10mm and moisture content less than 15% is mixed with 0-8% pulverized coal to enter the rotary kiln. Limonite fines are dried, magnetized, arsenic removed and desulfurized in the same rotary kiln, and the rotating speed of the rotary kiln is 0.8-1.5 rpm. The temperature in the roasting area of the rotary kiln is 800-50 ℃, and the temperature in the drying area is 350-0 ℃.
The calcining water treated in the above steps is cooled. After cooling, it is classified by the classifier, the returned sand is sorted by magnetic pulley, and the overflow is sent to the magnetic separator for magnetic separation by the concentration pump. The magnetic part is the final product iron concentrate. The limonite fine ore with low iron grade and high arsenic and sulfur impurities is blended with coal, dried and roasted, magnetized and removed arsenic and sulfur impurities in the same kiln. The process is simplified. The roasted ore is subject to magnetic separation after water quenching and classification. After magnetic separation, the magnetite fine powder with high iron grade, low arsenic and sulfur impurities is obtained. It is widely used for beneficiation of ores and waste residues containing weakly magnetic iron minerals.
Magnetite Beneficiation
Hematite Beneficiation
Limonite Beneficiation
Siderite Beneficiation