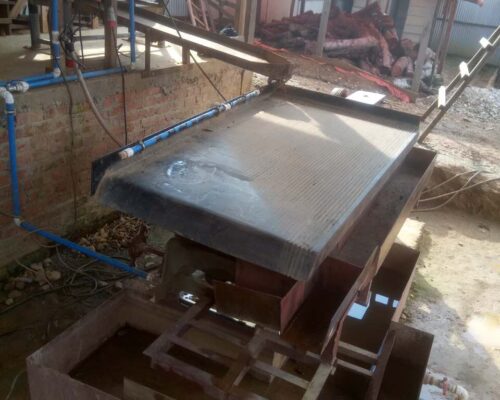
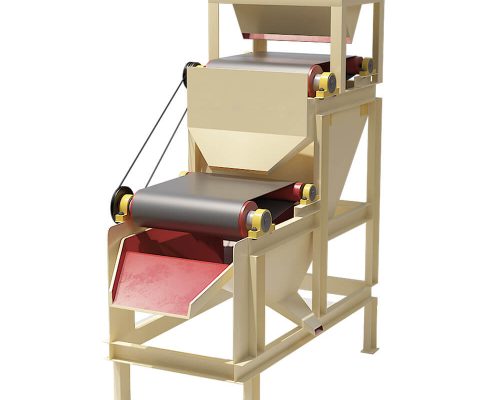
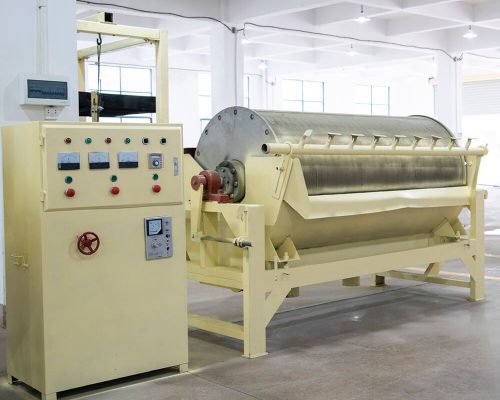
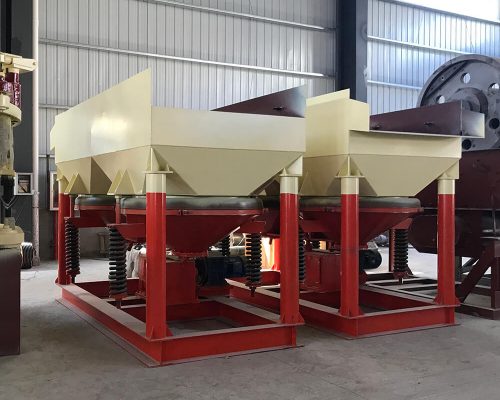
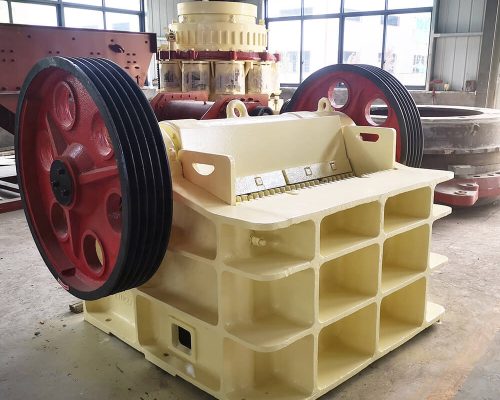
Manganese Ore Process
Most manganese ore is fine grain and contains phosphorus ore, iron ore, and associated minerals. According to its different principles, there are many methods to process manganese. And the magnetic concentration is the most widely used in manganese ore processing plants.
Introduction
Manganese (Mn) is the twelfth most abundant element in the Earth’s crust. Amongst some 300 minerals containing manganese, only about a dozen are of economic significance.
Manganese is a silvery-gray metal that resembles iron. It is hard and very brittle, difficult to fuse, but easy to oxidize. Manganese metal and its common ions are paramagnetic. Manganese tarnishes slowly in the air and oxidizes (“rusts”) like iron in water containing dissolved oxygen. The two main manganese minerals are pyrolusite (MnO2) and rhodochrosite (MnCO3).
Mineral Processing
Manganese Ore Processing
The commonly used manganese ore beneficiation methods are mechanical beneficiation methods (washing, screening, gravity separation, strong magnetic separation, and flotation), as well as special beneficiation methods (fire enrichment, chemical beneficiation, etc.)
Washing and Sieving
Washing is the separation of ore and mud under hydraulic, mechanical, and self-friction action, which improves the ore grade. Main ore washing equipment includes ore trommel screen, cylinder trommel scrubber, and tank washing machines.
The washing is often accompanied by screening, and the screen machine separates the cleaned ore into different sizes for use in different areas.
Gravity Separation
Gravity beneficiation is based on the difference in density and particle size of the mineral. The shape of the mineral particles affects the accuracy of sorting by density to some extent. Gravity separation can be used for concentrating, also for tailing processing and preconcentration. In addition, gravity separation generally consists of a combination process with magnetic separation and flotation.
The density of manganese oxide ore is generally about 3.7~3.9t/m3, which is significantly different from silicate type gangue. Commonly used gravity separators include mineral jigs, shaker tables, cyclones, chutes, and the like.
The density of manganese carbonate ore is 3.3~3.6t/m3, which has a small difference from the density of gangue. It needs to be separated by heavy medium separators.
Strong Magnetic Separation
Strong magnetic rough separation: Wipe out the waste by using a strong magnetic separator that specializes using in manganese ore, rough concentration of the concentrate by using a spiral classifier, rough concentration of the tailings drain to tailings thickener directly.
Classification: Underflow from the classifier is transported to a magnetic separator for concentration, the overflow will be concentrated by thickener.
Middle magnetic separation: The tailings from the middle magnetic separation drain to the concentrator, and the concentration from the middle magnetic separation get together with the underflow of the concentration.
Purification and concentration: Concentration overflow return to the system for cycling , concentration underflow get together with concentrate, to be the final separated concentrate.
The magnetic process is suitable for high phosphorus, high silica, and low iron manganese ore.
Manganese Ore Recovery Processing
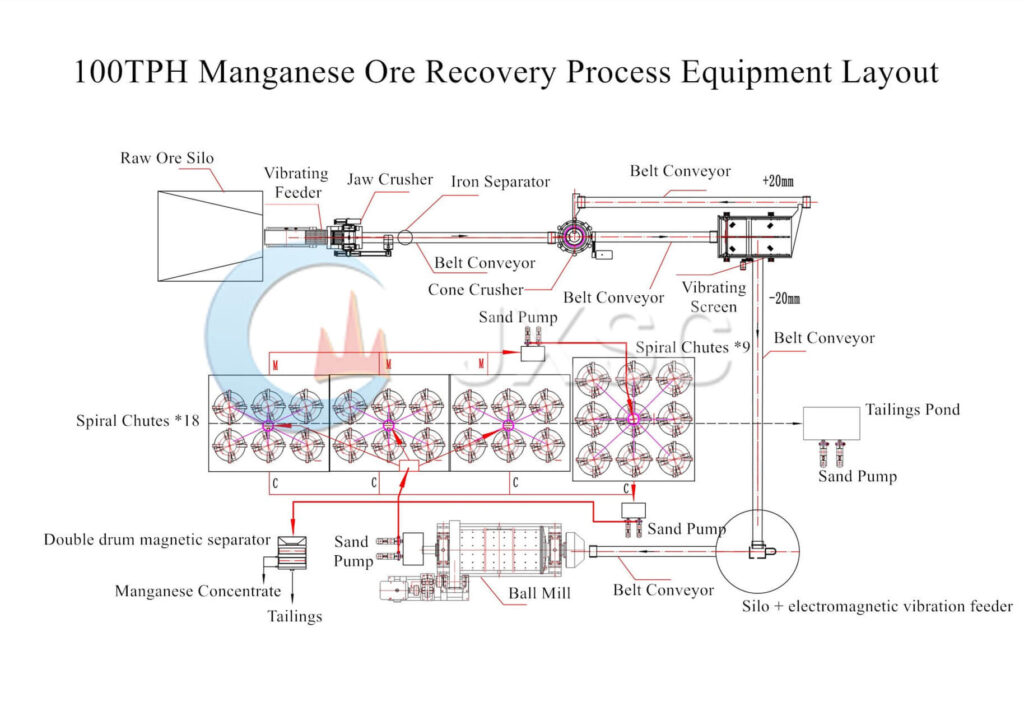
This setup is for the manganese ore process: raw bin+vibration feeder>jaw crusher>belt conveyor>cone crusher>belt conveyor>vibration screen>belt conveyor>hopper+electromagnetic feeder>belt conveyor>ball mill>slurry pump>spiral chute>slurry pump>double drum magnetic separator.
- The raw bin+vibration feeder for feeding materials to the jaw crusher automatically, you only need to load the materials to the raw bin by truck or excavator or else as you want.
- The jaw crusher is for crushing the raw ore into small pieces, then to the cone crusher to get the fine sizes.
- The vibration screen for separating the size +20mm back to the cone crusher, 0-20mm will to the hopper+electromagnetic feeder, then to the ball mill.
- The ball mill is for grinding the 0-20mm materials to 0-1mm, then using the slurry pump to transport the 0-1mm materials to the spiral chute to separate the heavy minerals.
- The double drum magnetic separator is for separating the manganese from other heavy minerals, making the manganese concentrate to a higher grade.
- The capacity for this washing plant can be customized as per request such as 10tph, 50tph,100tph, etc.,
Notes: The belt conveyor from jaw crusher to cone crusher will need to add the iron remover to make sure the safe and efficient work of the cone crusher.
The spiral chute will normally make two phases, the concentrate from the first phase spiral chute will to the second phase to concentrate again, which will make sure a higher grade and also release the workload of the magnetic separator.