Space on sand dredgers is limited, yet efficient mineral processing is necessary. The right jig machine makes all the difference between wasted potential and smooth operation. This guide shows you the smart solution for tight spaces.
Choosing a Circular Jig solves space constraints on sand dredgers. Its compact annular design fits perfectly while delivering high mineral recovery rates. Unlike rectangular jigs, the circular version processes material continuously without corners that slow down production. It uses less water and power, making it ideal for mobile dredging setups with limited space and resources.
Now let’s understand why this solution works so well. The circular jig wasn’t designed by accident. Its unique features come from solving specific challenges in marine mineral processing.
What is a Sand Dredger?
Imagine floating factories that extract precious minerals from riverbeds and sea floors. Sand dredgers do this heavy lifting but face constant space battles between equipment and storage.
A sand dredger is a floating combined mining and processing unit specifically designed to mine submerged sand deposits or loose materials. The sand dredger extracts the ore through the excavation mechanism installed in the flat-bottomed bow and lifts it to the silo on board. After screening, washing, and grading, the fine-grained material containing ore enters the rougher chute or jigger for roughing. At the same time, the tailings are discharged through the tailings chute or sand pumps to the mining area behind the stern of the vessel. The working deck holds all the processing machinery, including the jig separator, pumps, and classifier, making efficient use of limited space absolutely critical.
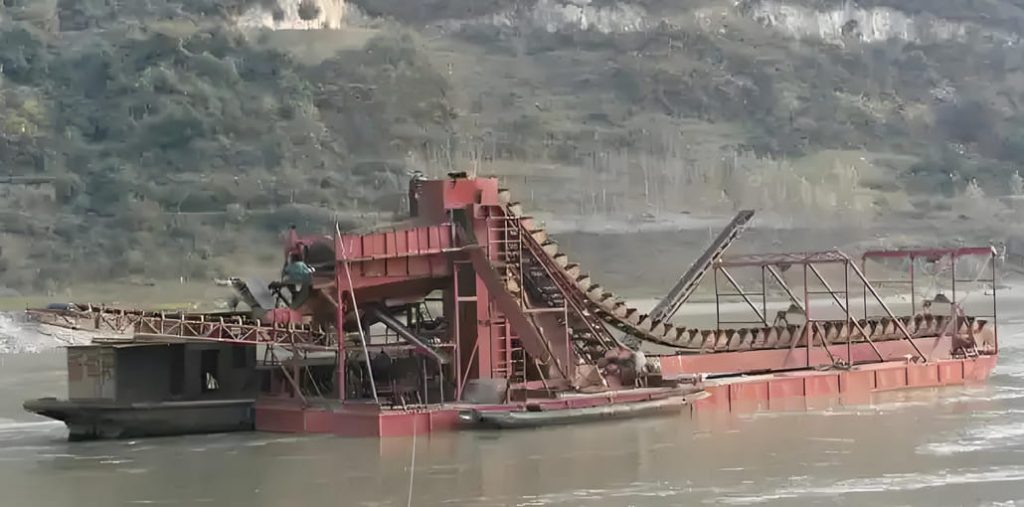
Application Scenarios, Advantages & Disadvantages
The sand mining dredgers are widely used in sand mining operations in various waters, including rivers, lakes, and reservoirs. Their advantages include large production capacity, high labor productivity, low cost, and ease of management. However, the conditions of use are more stringent, the initial equipment costs are higher, and they are not suitable for use in fast-flowing rivers or in mineral formations that are frozen all year round.
Core Components of Modern Sand Dredgers
Every sand dredger has three operational zones:
- Excavation Zone
- Cutter heads or suction pipes
- Hydraulic systems
- Sediment intake pipes
- Processing Zone
- Screening equipment
- Jig machines (primary separator)
- Secondary concentration devices
- Storage/Discharge Zone
- Mineral concentrate holds
- Tailings disposal system
Component | Space Required (m²) | Notes |
Excavation System | 15-20 | Fixed installation |
Primary Screening | 8-12 | Must feed directly to jigs |
Jig Machines | 10-18 | Largest processing footprint |
Pumps/Piping | 5-8 | Vertical stacking possible |
What is a Circular Jig?
Picture a mineral sorting system where every square centimeter works harder. That’s the circular jig – a game changer developed specifically to overcome marine mining challenges.
A circular jig is a mineral concentrator with an annular bed that pulses water through ore slurry. As the pulses happen, heavier minerals settle while lighter materials wash away. The continuous circular motion eliminates dead zones common in rectangular jigs, giving more separation in less space with lower water usage, typically 20-30% less than conventional designs.
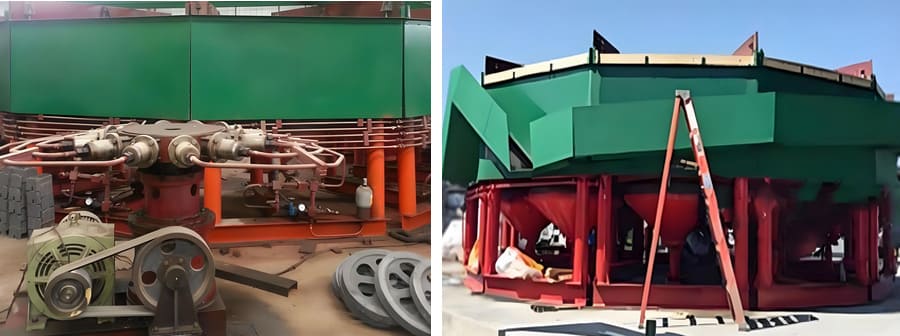
How Circular Jigs Maximize Limited Space?
The annular design creates three space-saving advantages:Efficient Footprint
- No corner areas that don’t contribute to separation
- Concentric layers allow for:
- Inner feed distribution
- Middle separation zone
- Outer concentrate collection
Modular Stacking Capability
- Multiple units can operate vertically
- Shared support structures reduce:
- Platform space needs by 40%
- Structural weight by 25%
Reduced Supporting Systems
- Single central drive mechanism
- Simplified water distribution
Feature | Circular Jig | Rectangular Jig | Advantage |
Footprint | 4-6m² | 8-10m² | 40-50% less space |
Water Consumption | 50 m³/h | 70 m³/h | 30% less water |
Drive Power | 5.5 kW | 7.5 kW | 25% energy saving |
Maintenance Access | 3 sides | 1 side | Easier servicing |
Why Choose Circular Jig When There is Lack of Space on Sand Dredger?
When decks get crowded and every machine fights for space, conventional equipment becomes a liability. Here’s why seasoned dredging operations switch to circular jigs.
Circular jigs outperform in tight spaces because their design eliminates wasted areas. The continuous circular flow processes ore 20-30% faster than rectangular jigs of comparable size. Their modular nature allows installation in corners or stacked configurations impossible with other designs, crucial when deck space costs thousands per square meter in vessel construction and operation.
The spatial adaptability advantage of circular jigs
- Compact integrated design
The circular jigs are composed of multiple trapezoidal jig chambers (such as the domestic YT-7750 type with 12 chambers) arranged in a ring. Although the diameter is 7750mm, the floor space can be flexibly adjusted through modular design (supporting 3-chamber, 6-chamber, and 9-chamber combinations). For example, only the 90° fan-shaped area (3 chambers) can be used to meet small-scale processing needs, significantly saving space. - Central feeding and radial flow field
After the slurry is fed from the center, it flows radially to the surrounding areas. There is no need to configure multiple feeding equipment or complex pipelines, which simplifies the pipeline layout on the sand mining ship. Heavy products are directly collected through the screen discharge, reducing the tailings transportation space required by traditional jigs. - High unit processing capacity
The unit screen surface processing capacity of the circular jig is 7~9t/(m²·h). A nine-chamber Ф7750mm device can process 220t/h of raw sand, which is equivalent to the efficiency of multiple small jigs, greatly reducing the number of equipment required.
Performance parameters and energy-saving characteristics
- Wide-level selection: materials below 25mm are allowed to be selected without classification, and the recycling limit is as low as 0.05mm (quartz meter), saving space for pre-treatment equipment.
- Save 60%~70% water: the water replenishment under the screen is only 1.2m³/t, reducing the area occupied by water pumps and water storage devices.
- Quick tailings discarding:80%~90% of the tailings can be discarded at one time in the rough selection of placer gold ore, reducing the load and space pressure of subsequent sorting links.
Calculating the Real Space Savings
Let’s examine a real installation scenario:- Traditional Approach (Rectangular Jigs)
- Requires 8m x 5m clear deck area
- Needs 1m maintenance walkways on three sides
- Total occupied space: ~55m²
- Circular Jig Solution
- 6m diameter units (28m² each)
- Can be placed against bulkheads (no walkway needed on one side)
- Stackable design allows two units in <40m² footprint
Layout | Processing Capacity | Deck Space Used | Space Efficiency Rating |
2 Rectangular | 100 tons/hour | 110m² | 0.9 t/h/m² |
2 Circular | 120 tons/hour | 56m² | 2.14 t/h/m² |
Stacked Circular | 180 tons/hour | 28m² | 6.43 t/h/m² |
The numbers prove circular jigs produce more mineral concentrate per square meter – exactly what space-constrained dredgers need. Their flexible installation also avoids interference with:
- Crane operations
- Conveyor paths
- Crew movement areas
- Emergency access routes
Conclusion
When deck space limits your sand dredger’s mineral processing capacity, circular jigs offer the smart solution. Their annular design packs more separating power into less space while using fewer resources. Modular circular jigs outperform rectangular models in processing rate, water efficiency, and installation flexibility – crucial advantages in marine mineral extraction. For dredging operators, choosing circular means gaining production capacity without expensive vessel modifications. The space savings alone often justify the equipment upgrade within a single season of operation.