Heap leaching has emerged as one of the most economically viable methods for extracting metals from low-grade ores in the mining industry worldwide, with China adopting and adapting this technology to its diverse geological and climatic conditions. This extraction process, which involves percolating leaching solutions through ore piles to dissolve target metals, offers significant advantages in terms of capital expenditure, operational flexibility, and environmental management compared to conventional processing methods. As China continues to develop its mineral resources across varying geographical regions—from the arid northwest to the humid southern provinces—mining operations have been compelled to innovate and customize their heap leaching systems to maximize efficiency while addressing unique regional challenges. This article explores the fundamental components of heap leaching systems, identifies the ore types most suitable for this processing method, and examines how Chinese mining operations have adapted their heap leaching regimes to overcome diverse climatic constraints across the country.
What is The Heap Leaching System?
Understanding the heap leaching system is like knowing the recipe before you start cooking. If you don’t know the steps – preparing the ore, stacking it, leaching, and processing the solution – things can go wrong quickly, leading to inefficiencies or safety issues. The heap leaching system is the sequence of operational steps involved in extracting minerals using this method. It typically starts with ore preparation (crushing, sometimes agglomeration), followed by stacking the prepared ore onto the lined pad. Then, the leaching solution is applied. The resulting pregnant leach solution (PLS) is collected and sent to a processing plant for metal recovery. Finally, the barren solution is recycled back into the heap, and spent ore is detoxified and reclaimed.
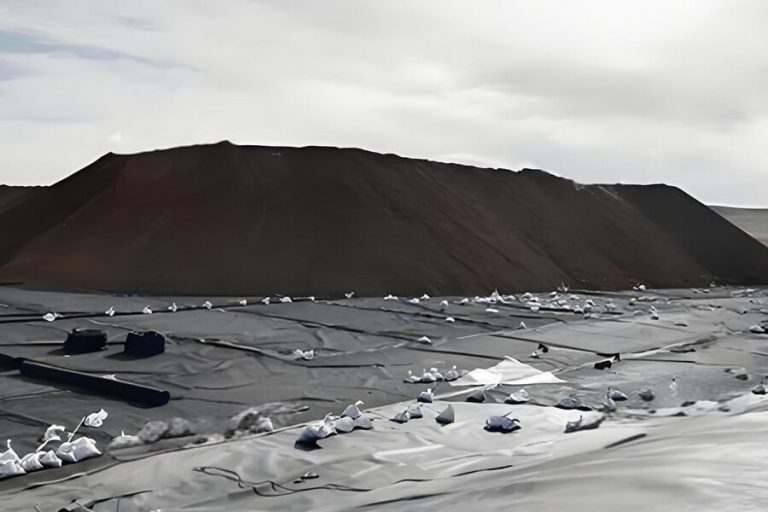
Defining the system helps everyone involved understand their role and how each step impacts the next. It forms the basis for operational procedures, training, and process optimization efforts. Let’s break down the typical cycle.
Core Components of a Heap Leaching System
Ore Preparation
- Mining: Extracting the ore from the pit or underground source.
- Crushing/Screening: Reducing the ore size to the optimal range determined by testing. This increases the surface area for leaching. Usually involves multiple stages (primary, secondary, tertiary crushing).
- Agglomeration (Optional but common for gold/silver and ores with fines): Mixing the crushed ore with cement, lime, and/or concentrated leach solution. This binds fine particles to coarser ones, improving heap permeability and preventing channeling of the solution.
Heap Construction (Stacking)
- Transport: Moving the prepared ore to the leach pad, typically via conveyor belts or haul trucks.
- Stacking: Carefully place the ore on the lined pad to the planned height. Methods include radial stackers or truck dumping, followed by dozer spreading. Care must be taken to avoid over-compaction, which reduces permeability and segregation of coarse/fine particles. Lifts (layers) are typically used.
Leaching
- Solution Application: Pumping barren or intermediate-strength leach solution to the top of the heap and distributing it evenly using the designed system (drips, sprinklers). Application rates are carefully controlled.
- Percolation: The solution slowly trickles down through the ore heap, dissolving the target minerals.
- Solution Collection: The PLS drains to the bottom of the heap, is collected by the pipe system, and flows to the PLS pond.
Solution Processing
- PLS Treatment: Pumping the PLS from the pond to the processing plant. Common recovery methods include:
Gold/Silver: Carbon adsorption (CIC/CIL), Merrill-Crowe precipitation.
2. Copper: Solvent Extraction and Electrowinning (SX-EW). - Metal Recovery: Extracting the dissolved metal from the solution to produce a final product (e.g., doré bars, copper cathodes).
- Barren Solution Regeneration: The solution, now stripped of the most valuable metal, is adjusted (e.g., reagent concentration) and sent to the barren solution pond for recycling back to the heaps.
Detoxification and Closure (End of Life)
- Rinsing: After leaching is complete, the heap is often rinsed with fresh water or a neutralizing solution to remove residual leach chemicals.
- Detoxification: Treating the heap material to meet environmental standards before closure.
- Recontouring/Reclamation: Reshaping the spent heap and covering it with topsoil/vegetation to blend with the landscape. This cycle represents the core operational flow. Effective management involves monitoring and controlling parameters at each stage.
This system is particularly valuable for processing low-grade ores that would be uneconomical to process through conventional methods.
Suitable Ores For Heap Leaching System
Heap leaching systems are suitable for processing low-grade, permeable ores, especially those that have become loose and porous after oxidation and weathering. Specifically, heap leaching systems are mainly suitable for the following types of ores:
- Low-grade oxidized ores: These ores are usually located on the surface and have low gold content, but gold is found in various forms, such as gold-bearing quartz veins and gold-bearing breccias. Gold with a high degree of oxidation, located in the gangue or mineral fissures, and gold with small particles and easy exposure are more suitable for heap leaching.
- Sulfide ores: Sulfide ores where gold is not closely associated with sulfide minerals are also suitable for heap leaching. This type of ore is characterized by relatively low gold leaching rates, but gold can still be effectively extracted by heap leaching.
- Vein or placer gold ores:Vein or placer gold ores containing tiny gold particles or gold particles with large specific surface areas are also suitable for heap leaching. These ores have better gold leaching effects after crushing.
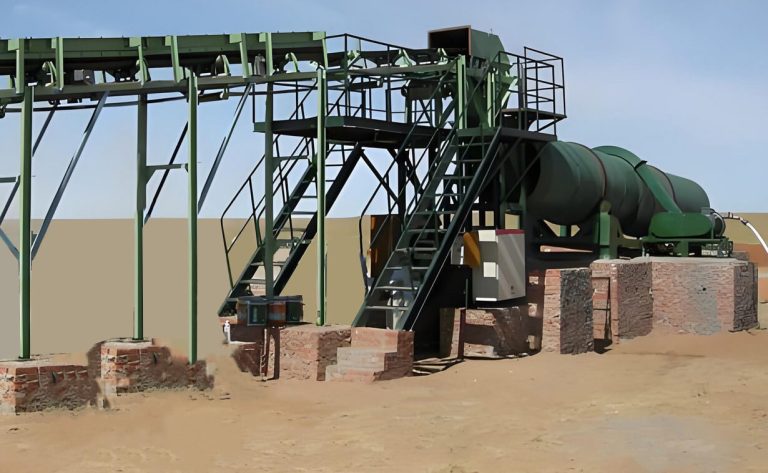
Heap Leaching Operating Regimes in China: Regional Adaptations to Climate Challenges
Climate Impact on Heap Leaching Operations
Heap leaching operations are primarily conducted outdoors, making them significantly affected by climate conditions. During adverse weather conditions such as rain, snow, or strong winds, maintaining normal heap leaching production becomes challenging. Southern China experiences prolonged rainy seasons, while northern regions have extended freezing periods, both of which reduce the effective working days for heap leaching operations.
Southern China Adaptation Strategies
Experience from southern mining operations shows that light rain has relatively minor impacts on production. Some mines have successfully maintained operations during rainy seasons (except during heavy storms) by implementing several strategies:
- Using rain-resistant membranes to cover heap leaching pads
- Enhancing flood prevention and drainage measures
- Improving solution pond management systems
Through these adaptations, mining operations in southern regions typically achieve approximately 300 working days annually.
Northern China Winter Operations
Maintaining normal production during freezing periods in northern regions presents significantly greater challenges. To address these issues, northern mines typically employ underground or covered heap leaching operations during winter months. Two main approaches are used for sprinkler and solution delivery systems:
- Ground-level installation with thick anti-freezing layers
- Underground installation at depths below 5 meters
When designing underground pressure solution pipes, particular attention must be paid to preventing low points where water could accumulate and freeze, potentially blocking the pipes. If topographical constraints make low points unavoidable, water release outlets and gate valves must be installed at these locations. As a result of these seasonal adaptations, heap leaching operations in northern regions typically achieve between 240 and 290 working days annually.
Customized Operating Schedules
The specific sprinkling regimes and operational schedules for different production phases should be established according to the characteristics of different mineral types and ore properties. Mines with adequate resources should conduct relevant tests to determine the optimal operating regimes for their specific conditions.
The evolution of heap leaching technology in China represents a remarkable example of adapting international mining practices to local conditions. By optimizing core system components, carefully selecting appropriate ore types, and implementing climate-specific operational strategies, Chinese mining companies have been able to extract value from resources that might otherwise remain economically unviable. The regional adaptations—whether protecting systems from southern monsoons or preventing freezing in northern operations—demonstrate the industry’s resilience and innovation. As environmental regulations continue to tighten and ore grades progressively decline, the importance of efficient, well-designed heap leaching systems will only increase. Moving forward, the integration of automation technologies, more precise hydrometallurgical controls, and enhanced environmental safeguards will likely define the next generation of heap-leaching operations in China, potentially establishing new global standards for this versatile extraction methodology. The continued refinement of these systems will be essential to sustaining China’s position as a leading mineral producer while meeting increasingly stringent sustainability requirements.