The arrangement and design of heap leaching facilities are critically dependent on terrain characteristics. Ignoring the site’s topography and geology can lead to significant operational inefficiencies, increased costs, structural instability, and severe environmental risks.
Why Terrain Characteristics Are So Important?
Slope and Stability
- Heap Stability: The natural slope of the ground significantly impacts the stability of the ore heap itself. Building on steep slopes increases the risk of landslides or heap failure, requiring extensive (and expensive) earthworks like benching or buttressing.
- Liner Integrity: The liner system beneath the heap must be placed on a stable, properly prepared foundation. Uneven or steep terrain makes liner installation more complex and increases the risk of tears or stress points due to differential settlement or slippage.
- Foundation: The underlying soil and rock must be capable of supporting the immense weight of the saturated ore heap. Geotechnical investigations are essential to assess foundation stability based on terrain and geology.
Hydrology and Drainage
- Solution Collection: Heap leach pads are designed with a slight, controlled slope on top of the liner to allow the pregnant leach solution (PLS) to drain efficiently via gravity to collection pipes and ponds. The underlying natural terrain often influences how this base slope is constructed.
- Surface Water Management: The surrounding topography dictates natural surface water runoff patterns. Facilities must be designed to divert rainwater and snowmelt away from the heap and process ponds to prevent dilution of solutions, overtopping of containment structures, and potential erosion or contamination. This often involves constructing diversion ditches and berms strategically placed based on the terrain.
- Groundwater Protection: The depth of groundwater and the direction of groundwater flow, often influenced by terrain, are critical factors in site selection and design to minimize the risk of contamination should a leak occur.
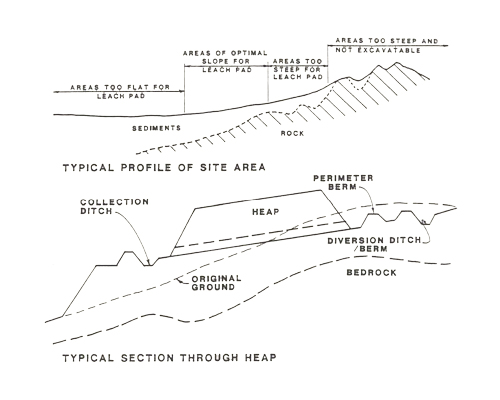
Operational Efficiency
- Gravity Flow: Utilizing natural slopes where possible can aid in the gravity flow of solutions, potentially reducing pumping requirements and energy costs.
- Ore Placement: The terrain affects how ore can be efficiently transported and stacked onto the heap using conveyors or trucks. Access roads and pad layouts are heavily influenced by topography.
Construction Costs
- Earthworks: Building on flat or gently sloping terrain generally requires less earthmoving (cut and fill) than building on steep or highly variable terrain, significantly impacting construction costs.
- Valley Fill Leach: Sometimes, a natural valley is used (a “valley fill” heap leach). This utilizes the terrain for containment on two or three sides but requires very careful engineering, particularly regarding foundation stability, liner systems, and managing water flow through the valley (both under the heap and around it).
Environmental Protection & Permitting
Regulators require detailed site assessments, including topographic surveys, geotechnical investigations, and hydrological studies. The facility design must demonstrate how it accounts for terrain characteristics to ensure stability and protect water resources.
In summary, while engineers can design facilities for various terrains, the specific characteristics of the site (slope, stability, drainage patterns) are fundamental inputs that dictate the layout, structural design, water management systems, construction methods, and overall feasibility and safety of a heap leaching operation. Site selection and design are iterative processes heavily guided by understanding and working with the terrain.
What Type of Heap Leaching Facility is Used For - Permanent or Multi-Lift Pad?
Heap leaching sites do not have high requirements for terrain conditions. They can be adapted to local conditions and set up a permanent heap leach pad or a multi-lift heap leach pad according to the terrain characteristics. For example, if the top of a mountain or a hillside is relatively gentle and open, it is appropriate to use it to build a permanent heap leach pad. The waste slag after each unloading can be pushed into the valley, and the yard area can be gradually expanded. If the ridge is steep and there is a relatively open and gentle site in the valley, a multi-lift heap leach pad(layered stacking pad) can be built at the bottom of the valley.
Most of the large heap-leaching mines today are built with superimposed ore piles in the valley. The bottom pad is assisted in the selected bottom layer. After a cycle of spray leaching is completed, the tailings are not discharged, and the newly mined ore is directly piled on it (the bottom pad can also be relaid after several layers). After the pile is built, a new round of spraying begins. This continues until it can no longer be piled up. When designing, the use of a multi-lift pad is given priority. A large number of production examples show that compared with permanent pads, multi-lift heap leach pads have the following advantages:
① Lower site leveling costs;
② Due to continuous heap leaching, the leaching rate is higher.
③ The operations of washing, dismantling, and transporting tailings can be omitted, and the production cost is lower.
④ The heap yard and the tailings yard are combined to reduce the pollution area.
However, it is usually difficult to build a road when building a heap yard at the bottom of the valley. Whether it is a permanent pad or a multi-lift pad, the mining road is a simple road. The road is usually developed along the edge of the heap yard, with the hillside on the inside and the heap yard on the outside. Drainage ditches are dug along the inner side of the hillside close to the road to drain the water from the mountain in the boundary area to the flood drainage ditch of the heap yard. With the expansion of the area of the multi-lift pad and the increase in the elevation, the access road to the mine and the flood drainage ditch are moved to the upper part of the hillside. For every 10m of the height of the heap yard, an appropriate safety platform should be left, and the heap yard slope should be kept at a certain angle. When the ore pile moves upward to a certain height, the lower safety platform and slope can be covered with soil for afforestation to restore vegetation and prevent soil erosion and mudslide accidents.
Regardless of the type of stockpile, the entire heap-leaching operation has multiple small stockpiles. Each small stockpile is equipped with a liquid collection ditch. Production experience tells us that it is best to set up a double ditch for the liquid collection ditch. At different leaching periods, the grade of the solution is determined to determine whether to inject it into the precious liquid pool or the intermediate pool. More than two solution pools should be built downstream of the entire stockpile. One is the precious liquid pool, and the other is the intermediate pool. Some also need to set up a lean liquid pool. The precious liquid pool can be divided into two parts: one side is the precious liquid pool, and the other side is the clarification pool. The precious liquid in the precious liquid pool is pumped or self-flowed to the adsorption (extraction) system. The lean liquid pool is used to store the lean liquid after adsorption or the raffinate after extraction, and is transported to the heap leaching site for spraying after adding reagents (cyanide or sulfuric acid, etc.).
In the past, some mines built precious liquid pools and intermediate pools at the lowest point downstream of the stockpile. During the rainstorm season, water directly passes through, resulting in pool flushing and overflowing, causing metal loss and environmental pollution. Given this, when designing, the solution pool should be located in a position away from the flood runoff line according to the terrain conditions, and flood drainage facilities should be built around the pool. Some small mine solution pools are welded with metal plates or polymer plastic plates. For large and medium-sized mines, due to the large volume of the solution pool, concrete structures can be used, pits can be dug according to the terrain conditions, and impermeable membranes or clay can be laid inside, which is fast in construction and saves investment. Many mines adopt this approach, which can prevent leakage in normal times and flushing in rainstorms.
A flood control pool with a certain volume must be set up downstream of the stockpile, otherwise, it will inevitably cause metal loss and environmental pollution during the rainstorm season. The flood control pool should be located at the downstream assembly point of the water collection range around the stockpile. Generally, concrete structures are not built, and they are constructed in the form of digging pits and laying impermeable membranes. Since the liquid in the flood control pool contains some metal ions, it is usually sent to the lean liquid pool as a spray liquid, forming a liquid circulation inside the dump, and usually, no wastewater is discharged. To meet the requirements of environmental protection, large-scale heap leaching sites and waste slag sites are equipped with sand and mud retaining dams at the downstream outlets. In the rainy season, water can be stored in the dam, which can serve as a flood control pool. When the heap leaching site and the waste rock site are in the same valley, the reservoir formed by the retaining dam downstream of the waste rock site can be used as a flood control reservoir for the heap leaching site, without the need to build another flood control pool, or a small flood control pool can be built upstream of the retaining dam for regulation (during the non-rainy season).
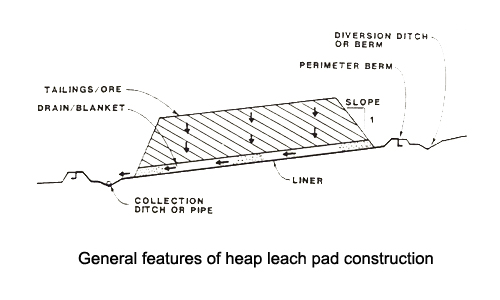
The choice of yard type depends on a variety of factors, including ore reserves, treatment capacity, ore nature, land availability and cost, environmental regulations, and trade-offs between capital and operating costs.
Conclusion
The design of a heap leach facility needs to optimize the layout based on terrain characteristics, and reasonably select a Permanent Pad, Dump-Leach Pad, or Multi-Lift Pad to ensure economy, safety, and environmental compliance.
Core principles: topography determines the layout, mine type, and size determine the type of pad, and economic and environmental requirements need to be evaluated in combination.