Heap leaching is a widely used technique in mining that can impact efficiency. Understanding how to design and optimize a heap leaching process is crucial. And if you get design indicators and process conditions wrong, it can lead to significant losses and inefficiencies. To determine heap leaching design indicators, assess factors like ore characteristics, leaching kinetics, and cost constraints. Consider both the physical and chemical attributes of the ore, as well as the economic factors that influence your design decisions to ensure successful implementation. To truly optimize heap leaching, we must explore these indicators and process conditions deeply. This ensures that we set ourselves up for success. Without focusing on details, we run the risk of poor performance, which we want to avoid.
How To Determine Heap Leaching Design Indicators?
Design indicators form the backbone of successful heap leaching. If you don’t get them right, everything can fall apart. Each project is unique, and understanding the nuances is essential. Design indicators for heap leaching include ore particle size, PH value, spraying intensity and time, sodium cyanide concentration, and type of yard. For example, low-permeable ores require a different approach than highly permeable materials, which should be taken into account during the design phase.
Indicators of heap leaching design
- Ore particle size: The heap leaching process requires the ore particle size to be between 10-30mm. Too coarse particle size will make it difficult to leach gold inclusions, while too fine particle size will block the pores. Therefore, the selection and commissioning of the crusher is crucial, and it is usually necessary to match the jaw crusher and cone crusher to achieve the target particle size.
- PH value: During the granulation process, the amount of lime needs to reach a pH value between 9.5 and 10.5. The appropriate alkalinity is determined through experiments to ensure the stability of the pellets in water. The amount of sodium cyanide also needs to be adjusted appropriately according to the humidity and impurities of the ore. Usually 60 to 150 grams of sodium cyanide is used per ton of ore.
- Spraying intensity and time: The spraying intensity is generally controlled between 6 and 20L/m²·h, and the maximum does not exceed 25 to 30L/m²·h. The spraying time is generally 7 to 8 hours a day, and no more than 10 hours at most. The spraying time should not be too long to avoid increasing the volume of the ore pile solution and affecting the gold leaching effect.
- Sodium cyanide concentration: The sodium cyanide concentration during spraying needs to be adjusted in time according to the gold leaching situation. The concentration can be controlled at 0.1% to 0.08% during the initial spraying. With the arrival of the peak leaching period, the concentration can be gradually reduced to 0.04% to 0.02%.
- Type of yard: The design of the yard should give priority to the stacking yard, which has the advantages of low site leveling cost, high leaching rate and low production cost compared to the permanent unloading yard. The stacking yard is directly stacked on the newly mined ore and a new round of spraying is carried out until it can no longer be piled up.
Dive deeper into heap-leaching design indicators
To dive deeper, we can break down the design indicators further. Here’s a simple table to visualize key indicators and their implications:
Design Indicator | Item | Requirement |
Ore property indicators | Particle size distribution | D80 particle size (particle size of 80% passing) is usually controlled at 5-25mm. If it is too fine, it needs to be granulated or pelletized. |
Mineralogical characteristics | The dissociation degree of the target mineral is >80%, and the content of harmful elements (such as As, Hg) must be <0.05%. | |
Permeability | K value (permeability coefficient) should be >10^-5 cm/s, and the optimal range is 10^-3~10^-4 cm/s. | |
Acid consumption/alkali consumption | In terms of CaCO3 equivalent, pre-neutralization should be considered when the acid consumption is >20kg/t. | |
Yard structure parameters | Pile height | Typical height 6-15m (lower limit for gold mines and upper limit for copper mines). |
Slope angle | dynamic pile 35-38°, static pile ≤32° (need to meet tanφ/cosβ>1.5 safety factor). | |
Bottom pad system | HDPE film thickness ≥1.5mm, permeability coefficient <1×10^-12 cm/s. | |
Leaching kinetics | Spray intensity | 5-15 L/(h·m²), higher for copper ore and lower for gold ore. |
Leaching cycle | 90-300 days for copper ore and 30-60 days for gold ore. | |
Leaching rate | Cu can reach 70-90% (secondary ore), Au needs to reach 60-85%. | |
Solution chemical control | pH value | cyanide leaching gold 10.5-11.5, acid leaching copper 1.5-2.5. |
Eh potential | gold ore -200~-400mV, copper ore +600~+800mV | |
Cyanide concentration | 0.05-0.3g/L (gold ore) | |
Fe³⁺ concentration | copper leaching needs to maintain >2g/L | |
Environmental control indicators | Anti-seepage system | double-layer liner + leachate collection, leakage <1 L/(ha·d). |
Solution balance | evaporation loss is about 3-8mm/d (up to 15mm/d in arid areas). | |
Pollution control | cyanide degradation rate>99.9%, Cu²⁺ concentration<0.5mg/L (emission standard). | |
Economic indicators | Tonnage processing cost | copper ore $2-5/t, gold ore $8-15/t. |
Infrastructure investment | $5-15/t ore processing capacity. | |
Metal recovery rate | boundary grade copper 0.15-0.3%, gold 0.3-0.8g/t. |
Key design points
- Heap leaching of copper ore: △[Cu²⁺] gradient >5g/L (injection-output).
- Heap leaching of gold ore: CN⁻/Au molar ratio >200:1.
- Heap temperature rise must be controlled to ΔT<15℃ (to prevent cyanide decomposition).
- The solution circulation rate should reach 80-95%.
In actual design, key parameters need to be obtained through column leaching tests. It is recommended to conduct at least 6 weeks of dynamic column leaching with 3 height gradients (1m, 3m, 6m), and use Pitard sampling theory to ensure sample representativeness. For complex ore bodies, it is recommended to use zoned heap leaching and a multi-stage countercurrent washing system.
Analyzing these indicators helps in determining the right leaching strategy. Higher ore grades directly translate to better recovery potentials, while the particle size determines how quickly the leachate penetrates. Meanwhile, permeability strongly affects the overall efficiency of the leaching process.
These fundamental design indicators set the stage for how effective your heap leaching will be. A solid understanding of them can save both time and money during project execution.
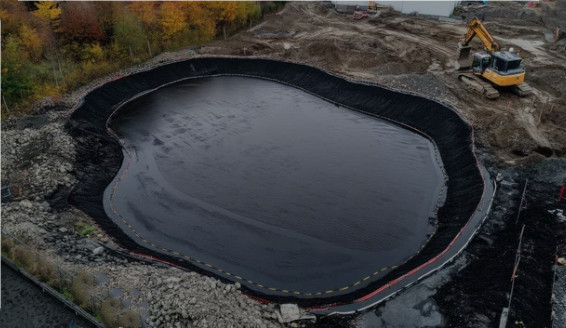
How To Determine Heap-leaching Process Conditions?
Once design indicators are established, the focus shifts to process conditions. These conditions can dictate the overall success of heap leaching. Therefore, knowing how to set these conditions directly impacts recovery and resource management. Process conditions for heap leaching include pH levels, temperature, and flow rates of the leachate solution. Maintaining ideal conditions leads to enhanced recovery rates and efficient use of resources, motivating developers to consistently monitor and adjust these parameters.
Dive deeper into the heap leaching process conditions
When refining the process conditions, it’s crucial to look at specific factors. Here’s a breakdown of conditions that may affect outcomes:
Condition | Importance | Optimal Range |
pH Level | Affects the solubility of metals | Generally bewtween 1.5 to 11 |
Temperature | Influences reaction rates | Ideally maintained between 20-80℃ |
Flow Rate | Determines the saturation level in heaps | Should be consistent and controlled |
The table above summarizes the key process conditions essential for heap leaching. Managing the pH level is vital for metal solubility, as deviations can negatively impact recovery. Temperature also plays a significant role since higher temperatures often increase reaction rates. Lastly, controlling the flow rate ensures the heap remains saturated without overwhelming it, keeping the leaching process efficient.
By paying attention to these process conditions, we create a more effective heap leaching operation. Continuous monitoring and adjustments can lead to sustained improvements and more profitable mining ventures.