The hydraulic roller crusher is mainly used to crush materials through the relative rotating motion of two rollers, to realize medium crushing, fine crushing, and sand making. It is a small sand-making machine, especially suitable for small and medium-sized stone plants. Compared with the impact sand making machine, the hydraulic roller crusher has a lower price, smaller output, low operating cost, and quick return on investment. In the process of operation and use, mastering some key safety operating procedures can protect the safety of the operator and extend the service life of the equipment. Following we will describe the safety operation guide of the hydraulic roller crusher.
Pre-startup Inspection
The hydraulic roller crusher must be inspected before startup to ensure the safe and stable operation of the equipment. Before each start-up, conduct a comprehensive equipment inspection, including the lubrication system, hydraulic system, drive belt and rollers, and other important parts. Make sure there is no looseness, wear, or damage, and pay special attention to whether there is any stuck material in the crushing chamber. If loose bolts, insufficient oil, or loose belts are found, they should be dealt with in time. The inspection items before starting the hydraulic roller crusher are as follows:
1. Equipment appearance check
- Check the appearance of the equipment for any abnormalities, such as oil leakage, loose bolts, or damaged parts.
- Check the surface of the rolls for wear, cracks, or attached foreign objects.
- Make sure there are no obstacles around the equipment and the working area is clean and tidy.
2. Lubrication system check
- Check whether the oil level of lubricating oil is normal and whether the oil is clean and free from pollution.
- Confirm that there is no leakage in the lubricating oil pipeline and joints.
- Check whether the lubrication pump or lubrication device is working properly.
3. Hydraulic system check
- Check whether the oil level of the hydraulic oil tank is within the specified range and whether the oil is clean.
- Check whether there is leakage or aging of the hydraulic pipeline and joints.
- Test whether the pressure of the hydraulic system is normal to ensure that the control system is sensitive and reliable.
4. Electrical system check
- Check whether the power supply is normal and the cables and wiring are not damaged.
- Check whether the electrical components in the control cabinet are intact and have good contact.
- Make sure that the operating devices such as the start button and emergency stop switch function normally.
5. Roller gap check
- Adjust the counter roll clearance to ensure that the clearance meets the processing requirements.
- Check whether the spring or hydraulic adjusting device is working properly to avoid the problem of too large or too small gaps.
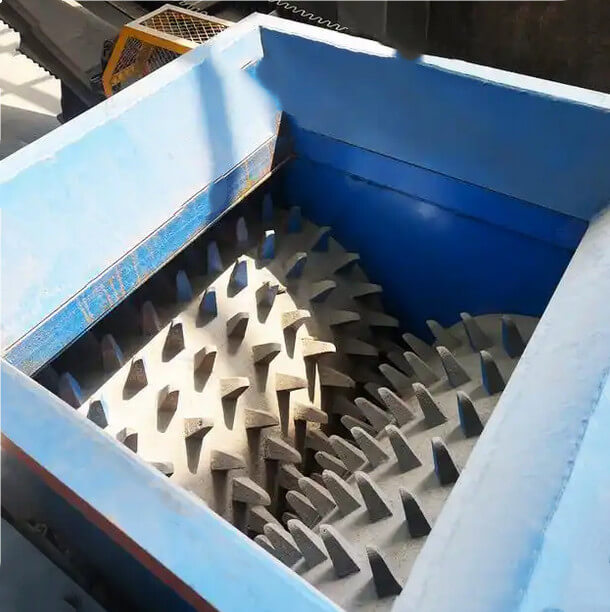
6. Transmission system check
- Check whether the transmission parts such as pulleys, chains, etc. are firmly installed without looseness or abnormal wear.
- Check whether the coupling between the motor and the equipment is centered to ensure smooth operation.
7. Protection device check
- Check whether the overload protection device and emergency stop device are intact and effective.
- Make sure the safety cover, guardrail, and other protective measures are installed in place.
8. Trial run check
- No-load test run, observe whether the equipment has abnormal vibration or noise.
- Check whether the starting process of the equipment is smooth and whether the operation of each component is normal.
After all checks are completed, the motor can be started. Only after the roller crusher enters into normal operation, it is allowed to add materials.
Work Precautions
Hydraulic roller crusher needs special attention to the following matters in the working process to ensure safe operation and efficient operation.
Operator Safety
- Wear protective equipment: Operators must wear suitable protective clothing such as dust masks, safety glasses, and non-slip shoes to prevent bodily injury from stone dust or other debris.
- Prohibit proximity to dangerous parts: When the equipment is running, personnel are strictly prohibited from being close to the roll area, transmission parts, and other running parts.
- Operating authority and protocol: Ensure that only professionally trained personnel with operating certificates can operate the equipment. It is strictly forbidden to change the parameters of the equipment or the operating procedures at will. Strictly observe the operating manuals and procedures provided by the manufacturer and follow the prescribed steps. Seek guidance when unfamiliar with the operating procedures.
- Emergency Stop Measures: Operators need to familiarize themselves with the emergency stop device to ensure that they can stop the machine quickly in case of abnormal conditions.
Material Management
- Uniformity of material: Ensure uniformity of material supply, do not supply too much or too little material at one time, to avoid uneven force on the rollers.
- Avoid hard foreign matter: Strictly prohibit metal blocks, stones, and other hard foreign matter into the equipment, so as not to damage the rollers or cause safety accidents. Install an iron removal device to avoid non-crushing materials (such as brazier heads, etc.) falling into the double rolls, damaging the crusher, and causing parking accidents.
- Material particle size control: Ensure that the particle size of the material entering the equipment meets the requirements to avoid clogging or equipment damage due to excessive particle size.
Tips:
- Keep the double-roll mobile bearing seat and guiding slide plane clean, so that when the machine is into the large pieces of material that can not be crushed, the movable crushing roll can back up to avoid.
- Iron removal work should be strengthened: install an iron removal device to avoid non-crushing materials (such as brazing head, etc.) falling into the double rolls between the crusher, and damage to the crusher, resulting in stopping accidents.
- Precautions to be taken when dealing with large materials: when the material to be dealt with contains a large number of large pieces, pay attention to the fact that large ores are easily extruded from the crushing space to prevent injury or damage to the equipment.
Operation Monitoring
- Equipment vibration: pay attention to observe whether there is abnormal vibration of the equipment, if there is any abnormality, it should be shut down immediately for inspection.
- Working Sound: Normal running sound should be maintained during operation, if abnormal sound occurs, shutdown for inspection is required.
- Hydraulic pressure: monitor the pressure of the hydraulic system at any time, and keep it within the rated range to prevent the working efficiency from being affected by too high or too low pressure.
- Bearing Temperature: Monitor the equipment bearing temperature, if the temperature is found to be abnormally high, you should check whether the lubrication is normal.
Tips
- Adjustment of discharge opening: After the roller crusher has been running for a while, due to the large wear of the roll surface, it will cause the product size to be too fine. At this time, attention should be paid to adjusting the discharge opening or overhauling the equipment.
- The bearing temperature should not exceed 65℃.
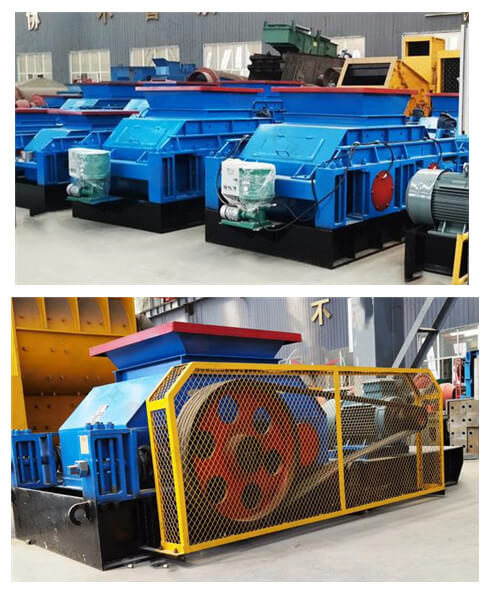
Lubrication and Heat Dissipation
- Lubrication system: Ensure the normal supply of lubricant to avoid the wear of parts due to insufficient lubrication.
- Oil quality monitoring: check the quality of lubricating oil regularly and replace it in time if it is found to be polluted or deteriorated.
- Heat dissipation effect: pay attention to the working condition of the equipment heat dissipation system to prevent the hydraulic oil temperature from being too high.
Overload and Blockage Treatment
- Avoid overload: pay attention to the current, hydraulic pressure, and running load at any time to prevent overload operation.
- Clear the blockage in time: if a blockage occurs, stop feeding immediately, and after the material in the equipment is discharged, shut down the equipment for cleaning.
Regular Inspection and Record
- Equipment inspection: Regularly check the wear and tear of wearing parts such as crushing tooth plate, axle tile, and mobile guiding slide of bearing seat, and replace them in time if necessary.
- Record operation data: Record the operation parameters of the equipment, such as hydraulic pressure, motor current, bearing temperature, etc., to facilitate the discovery of potential problems.
- Timely maintenance: abnormal wear and tear or loose parts should be found, and should be shut down in time for maintenance.
Precautions When Stopping The Machine
- Gradual shutdown: stop feeding the roller crusher 2~3min before stopping the machine, only when the material passes through the crusher, it is allowed to stop the machine.
- Clean up the equipment: Check and clean up the residual material in the equipment after stopping to avoid affecting the next startup.
- Hydraulic Pressure Relief: After shutting down the equipment, remove the pressure in the hydraulic system to prevent long-term high pressure from damaging the system.
Following the above precautions can effectively extend the service life of the hydraulic roller crusher while improving operational safety and efficiency.