The increasing demand for high-quality construction materials has made manufactured sand (M-sand) a sustainable and efficient alternative to natural river sand. A 100-ton-per-hour (TPH) sand-making plant is an ideal solution for mid- to large-scale sand production, offering automation, consistent output, and environmental benefits.
100 TPH Sand Making Plant
JXSC, a leading manufacturer of mineral processing equipment, has developed an optimized 100 TPH sand-making plant that integrates advanced crushing, screening, and washing technologies. This production line has been successfully deployed in multiple projects worldwide, delivering high-quality M-sand with excellent particle shape and gradation control.
This guide explores the sand-making process, key equipment, technical advantages, and economic benefits of investing in a 100 TPH sand manufacturing plant.
Why Choose Artificial Sand Over Natural Sand?
Natural sand mining has severe environmental consequences, leading to stricter regulations and supply shortages. M-sand, produced by crushing rocks, provides a superior and more sustainable alternative.
Key Advantages of M-Sand
- Environmental Sustainability
- Reduces illegal dredging of riverbeds, protecting aquatic ecosystems.
- Uses industrial waste (like quarry dust or slag) to produce sand, reducing landfill burden.
- Less dependence on diminishing natural sand reserves.
- Better Quality Control
- Artificially produced sand has a consistent grain size, shape, and texture, unlike natural sand, which varies in quality.
- Lower impurities (clay, silt, organic matter) ensure higher concrete strength and durability.
- Can be tailored for specific applications (e.g., fine or coarse gradation).
- Higher Strength in Concrete & Mortar
- Angular and rough-textured grains improve mechanical bonding in concrete.
- Reduces segregation and improves workability when properly graded.
- Enhances compressive strength and crack resistance in structures.
- Cost-Effective & Local Availability
- Produced near urban construction sites, reducing transportation costs.
- Natural sand is expensive due to scarcity and regulatory restrictions.
- Less wastage of materials with optimized production.
- Regulatory Compliance
- Many governments encourage or mandate M-sand to reduce riverbed mining (e.g., India’s sustainable sand mining guidelines).
- Easier to certify for construction standards (e.g., IS 383 in India).
- Reduced Shrinkage & Cracking
- Absence of organic impurities prevents weakening of concrete over time.
- Artificial sand reduces efflorescence (salt deposits on surfaces).
Artificial sand is increasingly the smarter, more sustainable, and economical choice for modern construction, especially where quality control and environmental protection are priorities.
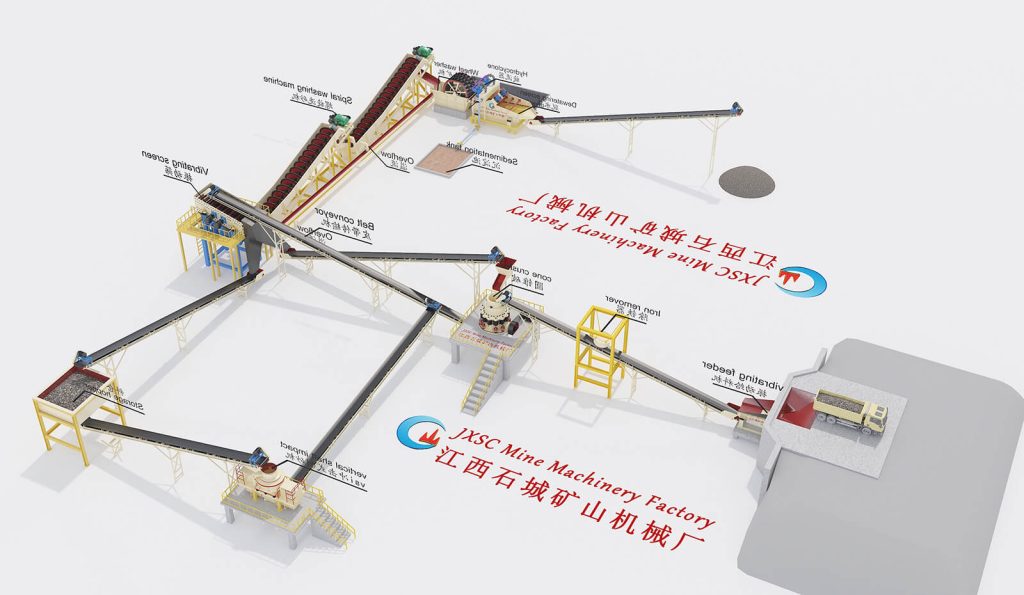
How Does The 100 TPH Sand Making Plant Work?
A fully automated 100 TPH sand plant consists of multiple interconnected stages:
- Raw Material Feeding (0-180mm input size)
- A vibrating feeder regulates the flow of crushed rock into the system.
- An electromagnetic iron remover detects and eliminates metal contaminants (critical for protecting crushers).
- A belt conveyor transfers material to the secondary crusher.
- Secondary Crushing (Cone Crusher or Impact Crusher)
- A hydraulic cone crusher further reduces material from 0-180mm to 0-35mm for optimal sand-making feed.
- A closed-circuit design recycles oversized (+35mm) material back to the crusher.
- This stage ensures uniform particle size before entering the sand-making machine.
- Sand Making (VSI Crusher – The Core Process)
- A Vertical Shaft Impact (VSI) crusher crushes and shapes the 5-35mm feed into 0-5mm fine sand.
- Rotor speed adjustment (45-75 m/s) allows control over particle shape (higher speed = finer sand).
- A cascade feeding system maximizes efficiency by distributing material evenly in the crushing chamber.
- Screening & Classification
A 3-deck vibrating screen separates sand into:
- 0-5mm (fine sand for plastering and masonry)
- 5-10mm (coarse sand for concrete and precast applications)
- Oversized material (recycled to the VSI crusher)
- Sand Washing & Dewatering (For High-Quality Sand)
Primary Spiral Sand Washer – Removes dust and clay.
Secondary Wheel Sand Washer – Further purifies sand, reducing moisture content.
Fine Sand Recovery System – Recaptures ultra-fine sand (<0.075mm) with 95 %+ efficiency.
Water Management:
- Cyclone separator recovers 80% of wash water for reuse.
- Sedimentation tanks ensure zero wastewater discharge.
- Dewatering screens reduce sand moisture to <15%, ideal for immediate use.
- Finished Product Stockpiling
- Conveyor belts transport washed sand to storage piles.
- Automated weighing & loading reduces manual handling.
Key Features of The Modern 100 TPH Sand Plant
- High Automation & Smart Controls
PLC control system adjusts crusher speed, feed rate, and water usage in real time.
Remote monitoring allows operational data tracking via mobile/desktop.
- Energy Efficiency
Variable frequency drives (VFDs) on motors reduce power consumption by 20-30%.
Eco-friendly dust suppression systems (fog spraying) minimize airborne particles.
- Customizable for Different Raw Materials
Granite, basalt, limestone, river pebbles – The plant can be configured for various hardness levels.
Construction waste recycling – Some plants integrate recycling crushers to convert demolition debris into sand.
- Compact & Modular Design
Pre-assembled modules reduce installation time.
Small footprint (5,000 sq. m or less), making it feasible for urban and rural sites.
Economic Benefits of The 100 TPH Sand Plant
High Return on Investment (ROI)
- Payback period: 18-24 months (with high sand demand).
- Production cost: $5-8 per ton (far cheaper than imported river sand).
Stable & Scalable Production
- Continuous operation (20+ hours/day capability).
- Easily upgradable to 150-200 TPH with additional modules.
Reduced Logistics Costs
- Local manufacturing eliminates long-distance sand transportation.
Is a 100 TPH Sand Making Plant Worth It?
For construction firms, mining operators, and infrastructure projects requiring consistent, high-quality sand, a 100 TPH sand plant is a profitable and sustainable choice.
✔ Higher quality sand than natural river sand.
✔ Fully automated, eco-friendly operation.
✔ Fast ROI due to strong market demand for M-sand.
Conclusion
The shift toward high-quality manufactured sand (M-sand) is transforming the construction industry by offering a sustainable, reliable, and cost-effective alternative to dwindling natural sand resources. As demonstrated in JXSC’s 100 TPH sand making plant, modern sand production technology ensures precise particle shape control, efficient gradation adjustment, and minimal environmental impact, making M-sand a superior choice for concrete and infrastructure projects.
With advanced automation, energy-efficient crushing processes, and intelligent washing systems, JXSC’s 100-ton-per-hour production line delivers consistent, high-grade M-sand while maximizing operational efficiency. Whether for large-scale construction projects or commercial sand supply, this system represents a smart investment in sustainable material production.
By adopting JXSC’s engineered solutions, producers can meet rising market demands while adhering to strict environmental regulations, proving that mechanized sand production is the future of the industry.