Gravity separation is an ancient physical separation method that uses the density difference between different minerals and external forces such as gravity to separate and extract useful minerals.
Before the 1980s, gravity separation was one of the most important separation methods for mineral extraction in China. In recent years, with the development and application of mineral separation technologies such as flotation and high-intensity magnetic separation, the importance of gravity separation has declined. However, gravity separation is still an important separation method for mineral separation and extraction in China, with its advantages of cleanliness and low consumption.
Flowing film gravity separation and spiral separation equipment
Flowing film gravity separation is a gravity separation method in which minerals are separated in a very thin (several millimeters) slurry flow layer, and is the main method for gravity separation of fine-grained minerals. Spiral beneficiation equipment (spiral chute, spiral concentrator, spiral separator) is a widely used flow film gravity beneficiation equipment, and also a kind of inclined flow beneficiation equipment. It is the key equipment for the beneficiation of hematite, ilmenite, chromite, specularite, tantalum-niobium ore, seashore placer, and coal, and is widely used in industry. According to rough estimates, the number of large and small spiral beneficiation equipment used in China’s industrial production can reach more than 100,000 sets.
The Development History of Spiral Concentrator
Spiral concentrator is a general term for spiral concentrator, spiral chute, and spiral separator. Conventionally:
- A foreign spiral concentrator with an elliptical cross-section is called a spiral concentrator.
- Chinese spiral concentrator with a cubic parabola cross section is called a spiral chute.
- In the field of coal washing, it is called a spiral separator.
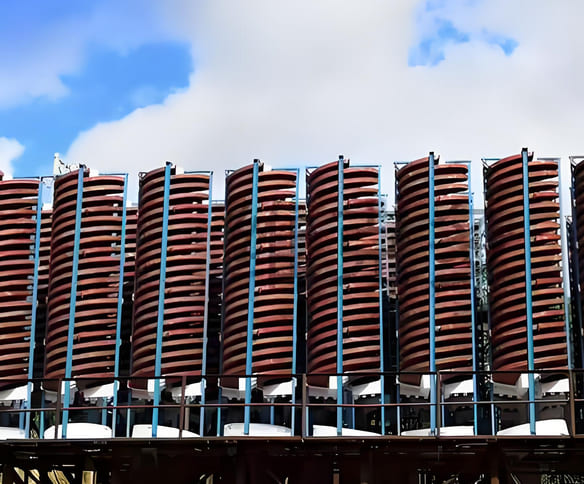
Development of Foreign Spiral Ore Dressing Equipment
- Technological germination (1941-1960)
- In 1943, Humphreys of the United States invented the first commercial spiral ore dressing machine. It adopts a single-head configuration, with a spiral groove diameter of 609.6 mm, a pitch of 342.9 mm, 5 to 7 turns per head, and is made of cast iron lined with rubber.
- In 1955, the Soviet Union developed the СКВ-2 type for the beneficiation of platinum group metals in the Urals.
- The golden age (1970-1990)
- In 1978, the Australian Reichert conical spiral was introduced, and the processing capacity increased by 30%.
- In 1989, the German KHD company launched a double-headed spiral with a sorting efficiency of 82%.
- Modern innovation (after 2000)
- In 2014, Canada’s Sepro Mineral Systems developed the Falcon SB series, a centrifugal force-enhanced type.
- In 2022, the British GTEK cooperated with the University of Cambridge on nano-coating technology, with a service life exceeding 12,000 hours.
Other foreign equipment: double-headed fiberglass spiral concentrator of Sweden’s Sara Company, CARPCO CS2000 spiral concentrator of Finland’s OUTOTEC Company (maximum diameter 940 mm), LD series spiral concentrator of Australia’s Roche Company, SX and SC series spiral concentrators of South Africa’s MULTOTEC Company, etc.
Development of Spiral Ore Dressing Equipment in China
- Initial stage (1950-1970)
- In 1955, the Guangxi Metallurgical Bureau Research Institute began to study spiral ore dressing machines and tested cement, cast iron, ceramics and other materials.
- In 1974, Fan Xiangbo and others from Beijing Research Institute of Mining and Metallurgy developed the LL1200 spiral chute (diameter Φ1200 mm), which used a cubic parabola cross-section curve and was successfully applied to the re-selection of fine-grained hematite in Anshan Iron and Steel.
- Technological breakthrough period (1980-2000)
- In 1989, Li Kaigong of Beijing Mining Institute developed the DL2000 spiral chute (diameter Φ2000 mm, currently the largest in the world), which used an “ellipse + cubic parabola” composite cross-section curve for the gravity separation of coarse particles of tin ore.
- In 1999, the BL1500 series spiral chute (diameter Φ1500 mm) was developed to solve the problem of recycling fine-grained minerals after large-scale production.
- Intelligent transformation (2010 to present)
- In 2016, the first machine vision sorting system of China University of Mining and Technology was applied in Panxi Vanadium Titanium Iron Mine.
- In 2023, CITIC Heavy Industries’ “Smart Spiral” realized 5G remote control and was selected into the “Smart Mining Equipment Catalog” of the Ministry of Industry and Information Technology. Current level: Maximum diameter of 2.4m (LY-2400 model); AI sorting accuracy ±0.02mm; Energy consumption per ton is 55% lower than that of traditional models.
Other domestic equipment:
- Rifle spiral chute of Anshan Iron and Steel Mining Research Institute (1982);
- Rotary spiral chute of Xinjiang Nonferrous Metals Research Institute (1986);
- GL series spiral concentrator of Guangzhou Nonferrous Metals Research Institute (1992);
- Multi-stage spiral chute of Liu Xuehai et al. of Beijing Mining Institute (1993);
- ZK-LX1100 spiral concentrator of China University of Mining and Technology (for coal washing).
China’s development and application technology of spiral chutes is currently at the forefront of the world, and a large number of equipment are exported abroad every year.
Spiral Chute Detailed Introduction
Structure
- Spiral trough: Usually made of fiberglass, plastic, or wear-resistant rubber, with 3 to 5 turns of spiral (vertical height of about 1 to 3 meters), and elliptical or parabolic cross-section.
- Feeding device: Located at the top, evenly feeds the slurry (a mixture of ore and water) into the trough.
- Flushing water system: Some models incorporate a flushing water system into the inner wall of the trough to enhance the sorting effect.
- Receiver/separator: Multiple outlets are set at the bottom to collect mineral products of different densities.
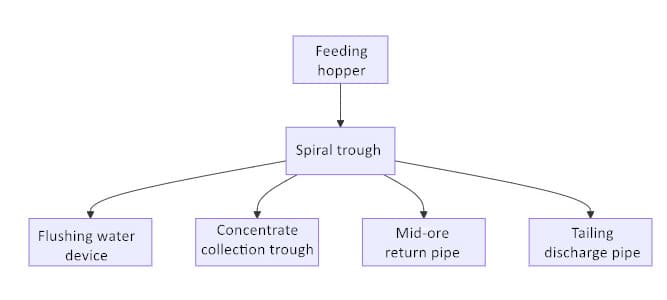
Working Principle
The working of the spiral chute is based on the composite separation mechanism of centrifugal force + gravity + friction. The specific process is as follows:
1. Slurry feeding
The slurry is fed evenly from the top of the spiral chute and flows downward along its length.
2. Centrifugal separation
Due to the rotating flow of the spiral chute, the particles are affected by centrifugal force (F=mv²/r):
- High-density mineral particles (such as gold, tungsten, iron ore) tend to the inside (more affected by gravity and friction)
- Lightweight gangue particles (such as quartz, feldspar) are pushed to the outside (more affected by centrifugal force)
3. Secondary circulation effect
The slurry forms a lateral circulation (Ekman flow) in the spiral chute:
- The upper slurry moves outward
- The lower slurry moves inward
This movement strengthens the stratification of minerals by specific gravity and improves the separation efficiency.
4. Intercepting and zoning
Finally, minerals of different densities form clear zones at different positions in the tank:
- Innermost layer (high-density concentrate, such as iron ore and titanium ore)
- Middle layer (medium-density minerals, which can be refluxed or reselected)
- Outermost layer (low-density tailings, such as quartz and mud)
5. Product collection
Minerals in each layer are separated by intercepting plates or separators, and the concentrate is discharged separately, while the tailings are directly discharged as waste.
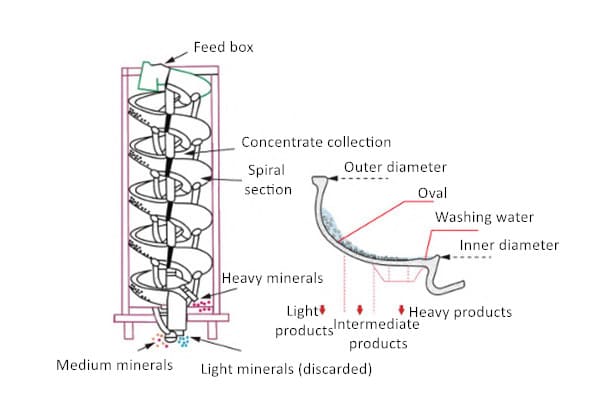
Core Features & Advantages
Simple structure, easy maintenance
- No power components, no motor drive required.
- The tank body is made of wear-resistant materials (such as polyurethane, ceramics) to reduce wear.
- Modular design, easy to replace and install.
High efficiency sorting, widely applicable
- Can be used for grading and sorting of 0.02~2mm ore particles.
- Adapt to minerals of different densities (such as iron ore, tungsten ore, tin ore, gold ore, etc.).
- Can process low-grade ores, with an enrichment ratio of 8~20 times.
Energy saving and environmental protection, stable operation
- Relying only on gravity and slurry flow, energy consumption is extremely low.
- No need to add chemical agents, reducing environmental pollution.
- Suitable for continuous production, high stability.
Strong adaptability
- Can match different slopes (6°~15°).
- Adjustable flushing water volume (10~50L/min).
- Can adapt to different slurry concentrations (20%~40% solid content).
Typical Application Scenarios
- Gold placer pre-selection (recovery rate can reach more than 85%).
- Iron ore sorting (rough selection of red ore and ilmenite).
- Tungsten-tin ore selection (cooperating with the shaking table to improve the grade of concentrate).
- Seaside placer processing (separation of titanium, zirconium, and rare earth ores).
- Tailing recovery (extracting residual minerals from old tailings ponds).
Spiral Chute vs Spiral Concentrator vs Shaking Table
Item | Spiral Chute | Spiral Concentrator | Shaking Table |
Working Principle | Gravity + centrifugal force | Gravity + centrifugal force | Reciprocating vibration + water flow impact |
Power requirements | Unpowered | Unpowered | Requires motor drive (high energy consumption) |
Applicable particle size | 0.02~2 mm | 0.1~5 mm | 0.02~0.2mm |
Enrichment ratio | 8~20 times | 5-12 times | 10~50 times |
Processing capacity | 3~8 t/h
| 2~5 t/h | 0.5~2 t/h |
Maintenance cost | Low | Low | Higher |
Spiral chutes usually do not have flushing water and rely on the natural flow of slurry for sorting, which is suitable for finer particle sizes; while spiral concentrators have higher sorting accuracy by adding flushing water, but the processing capacity is smaller.
Conclusion
The spiral concentrator, as a highly efficient gravity separation equipment, plays an indispensable role in mineral processing—such as iron, tungsten, and tin ores—thanks to its unique spiral chute structure, energy-free separation principle, low energy consumption, and easy maintenance. From its development history both domestically and internationally, China has achieved a transition from technology introduction to independent innovation, with notable breakthroughs in large-scale and intelligent design. Looking ahead, with the deepening of green mining initiatives and increasing demands for separation precision, spiral concentrators will further enhance wear-resistant materials, optimize automated control systems, and expand into emerging resource sectors like rare earths and lithium spodumene. This evolution will provide a more efficient and environmentally friendly solution for global sustainable mining development.