Mining operations lose millions yearly due to inefficient gold recovery. Modern processing plants now achieve over 95% recovery rates through optimized mineral liberation and separation.
Gold ore processing relies on four core systems working together: crushing/pre-sorting, grinding/classification, separation processes, and metal recovery. Each stage must be precisely calibrated to the ore’s specific characteristics. Through our proprietary process optimization models, we design plants that maintain 93-97% recovery rates even with complex ore types.
The difference between profitable and marginal operations often comes down to process choices. Let’s examine how each system contributes to final recovery rates.
Quicky View This Article
Crushing and Pre-processing Systems
-For efficient ore dissociation and cost control
Setting up a crushing and pre-sorting system at the front end of the beneficiation process can significantly improve ore dissociation and reduce subsequent milling energy and cost, especially for high-value minerals such as gold. Key technologies and optimization strategies for this system are described below:
1. Crushing process optimization – multi-stage closed-circuit crushing
(1) Core equipment combination
- Rough crushing: Jaw crusher (feed size ≤1m, discharge ≤150mm.
- Medium crushing: cone crusher (discharge ≤ 30mm, wear-resistant liner life optimization).
- Fine crushing: High-Pressure Roller Mill (HPRG) or Vertical Impact Crusher (discharge ≤ 10mm, energy saving 30%-50%).
(2) Closed-circuit screening control
- Screening equipment: high-frequency vibrating screen (wet screen anti-clogging), banana screen (large handling capacity).
- Cyclic loading rate: control 15%-25%, to avoid over-crushing.
- Intelligent regulation and control: online particle size analyzer + PLC automatically adjusts the crusher discharge port.
(3) Application advantages of High Pressure Roller Mill (HPRG)
- Energy saving: replace the traditional three-stage crushing, and reduce grinding power consumption by 20%-40%.
- Microcrack generation: Enhance the subsequent cyanide leaching rate (gold recovery rate increased by 3%-8%)
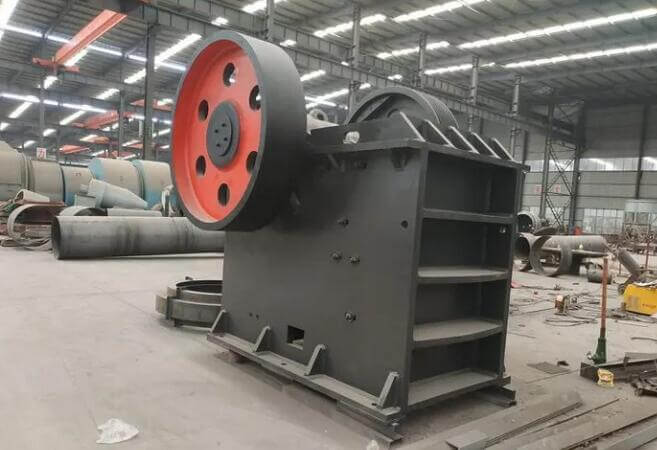
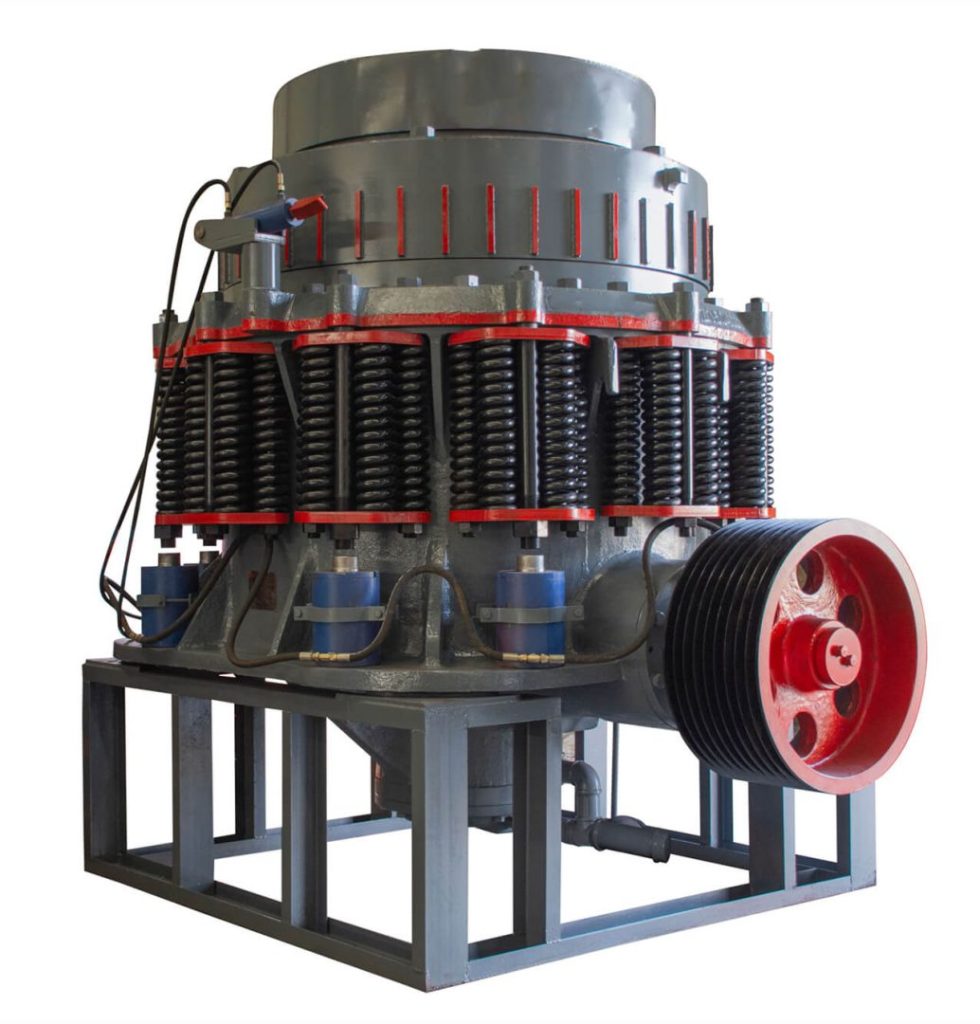
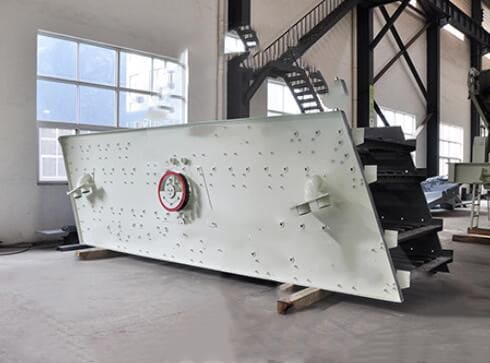
2. Pre-sorting and waste disposal technology – the core of low-cost consumption reduction
(1) XRT Intelligent Sorting (X-ray Transmission)
- Applicable ore types: Ores with a big difference in density/atomic number between veinstone and gold ore (e.g., quartz vein type).
- Effect: 30%-50% throw-away rate, gold loss rate <5%, directly reduces the amount of grinding ore.
(2) Heavy Media Cyclone (DMS)
- Density threshold: 2.8-3.2g/cm³ (for medium-coarse embedded gold).
- Economy: $1-$3 per ton of ore processing cost, can throw off 20%-40% of waste rock.
(3) Photoelectric sorting (laser/near-infrared)
Scenario: fast sorting of oxidized ore and sulfide ore (e.g., limonite with gold vs waste rock)
3. Early recovery of coarse gold – reduce the loss of “tailing”
(1) Jigger + shaking table combination
- Jigger: process -10mm ore, recover >0.1mm free gold (10%-30% of the total).
- Shaking table: gravity separation of the jig concentrate, and increase the gold grade to 100-500g/t.
(2) Flash flotation (in the grinding circuit)
- Equipment: small flotation tank (processing cyclone sediment).
- Function: Capture the dissociated coarse-grained gold and avoid over-grinding sludging.
4. Key Cost Control Indicators
Segment Unit | Cost ($/t) | Potential for Cost Savings |
Conventional three-stage crushing | 1.5-2.0 | 30% reduction by switching to HPRG |
XRT | 0.8-1.2 | 15%-20% reduction in milling costs for every 30% of waste thrown away |
Coarse gold recovery | 0.5-1.0 | 5%-10% reduction in tailings gold loss |
5. Crushing Efficiency Determines Downstream Performance
A single poorly configured crusher can reduce overall recovery by 8-12%. Proper size reduction ensures optimal mineral exposure.
Primary crushing should reduce ore to 80-150mm, followed by secondary crushing to 10-30mm. We install pre-sorting sensors that reject 15-40% waste rock before grinding, significantly reducing energy costs. The crushing circuit typically consumes 25% less power when using our automated gap adjustment technology.
Crushing Stage Optimization
Parameter | Standard Practice | Optimized Setup | Improvement |
Feed Size | 500mm | 300mm | -40% wear |
Closed-side Setting | 50mm | 35mm | +22% yield |
Throughput | 200tph | 240tph | +20% capacity |
Liner Lifetime | 800 hours | 1,200 hours | +50% longevity |
The crushing subsystem demands careful equipment matching. Jaw crushers handle initial size reduction best, while cone crushers provide finer control. We’ve found that installing metal detectors upstream prevents $15,000-$40,000 in crusher damage annually.
Ore type determines the optimal crushing approach:
- Free-milling ores: Two-stage crushing suffices
- Refractory ores: May require tertiary crushing
- Clay-rich ores: Need scrubbing systems to prevent clogging
Grinding and Classifying Systems
-The Key to Balancing Size Distribution and Energy Consumption
Overgrinding wastes energy; undergrinding leaves gold locked in particles. Finding the perfect balance separates profitable operations from strugglers.
The optimal grind size ranges between 75-150 microns, depending on gold dissemination. Our mills achieve this with 30% less energy than conventional designs through patented liner profiles and real-time particle size monitoring. The grinding circuit typically accounts for 40-60% of total plant energy consumption.
Grinding Optimization Parameters
1. Mill Speed
- 70-80% critical speed for optimal impact
- Variable frequency drives save 15-25% power
- Media Composition
- Forged steel balls for coarse grinding
- Ceramic media for fine grinding (last 20% size reduction)
- Classification Efficiency
- Hydrocyclones should achieve 85 %+ efficiency
- Poor classification can reduce recovery by 5-15%. We implement advanced control systems that:
- Adjust mill feed rate based on power draw
- Monitor pulp density in real-time
- Automatically balance circulating loads. Typical improvements our clients see:
- 18-22% reduction in grinding media consumption
- 12-15% lower energy costs
- 3-5% higher gold recovery
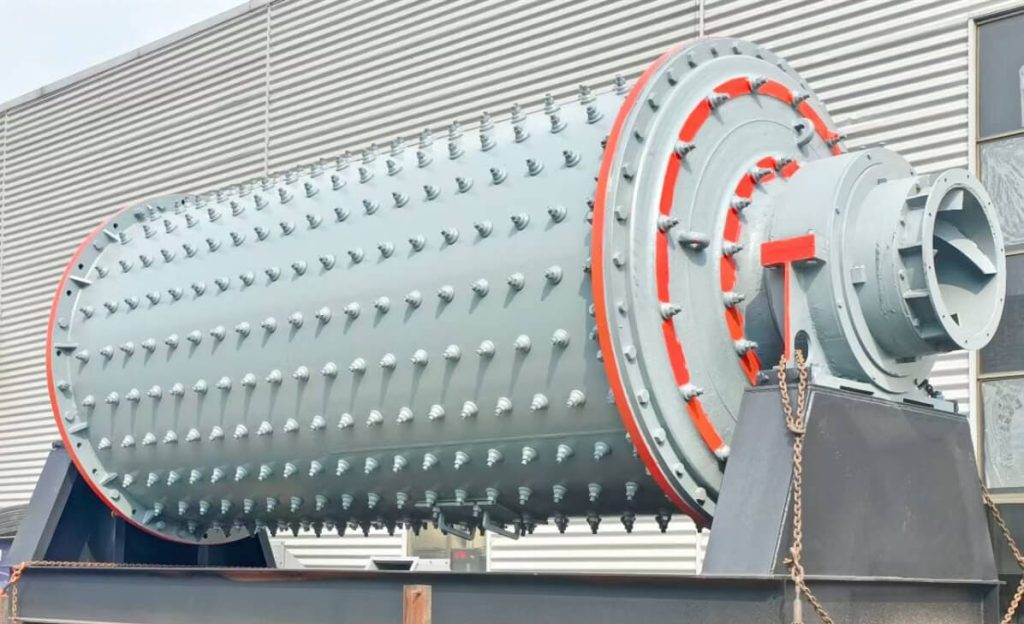
Equipment type | Power Configuration | Product index | Electricity consumption standard in 2025 |
Semi-autogenous mill | 2500kW | -5mm 92% | ≤10.5kW-h/t |
Vertical agitator mill | 315kWx4 | -200 mesh ≥93% | ≤6.5kw-h/t |
Separating Process System
-Selection of optimal paths by mineralization status
Choosing the wrong separation method can leave 20% of the gold in the tailings. The mineralogy determines the optimal approach.
Gravity separation recovers 30-60% free gold before leaching. Flotation captures 85-95% sulfide-associated gold. Cyanidation achieves 92-98% dissolution for free-milling ores. Our hybrid flowsheets combine methods to achieve 95 %+ overall recovery, significantly better than single-method plants averaging 85-90%.
1. Gravity Separation System
- Applicable conditions: coarse free gold (>100μm)
- Nelson concentrator: single machine capacity 50t/h, enrichment ratio 3000-8000 times
2. Flotation system
- Pharmacy system: butyl yellow drug (60g/t) + alcohol foaming agent (20g/t)
- Key index: concentrate gold grade 45-80g/t, recovery rate 88-92%.
3. Cyanide leaching system
- Leaching control: pH=10.8±0.2
- NaCN consumption: ≤0.30kg/t.
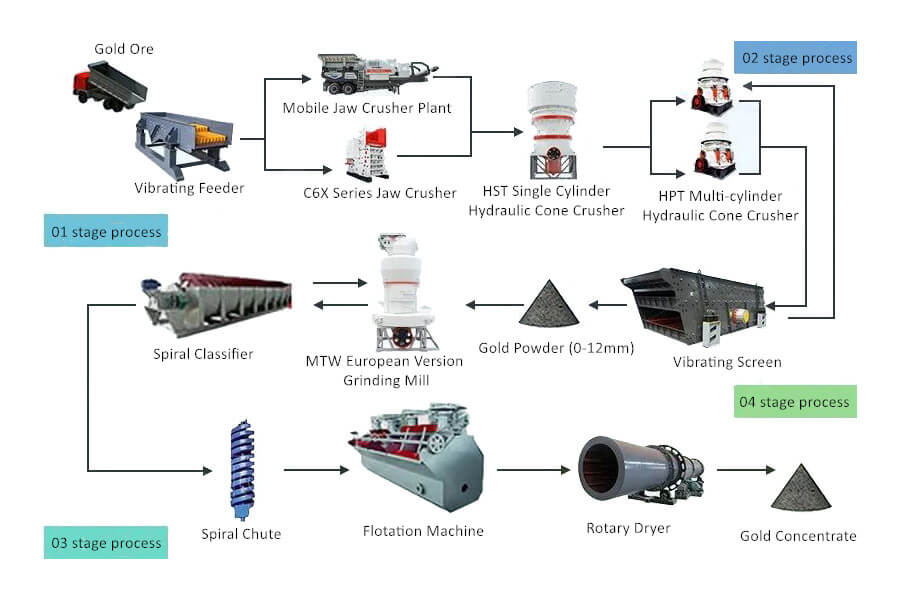
Separation Method Selection Matrix
Ore Characteristic | Preferred Method | Recovery Range | Cost (USD/ton) |
Coarse free gold | Gravity | 35-65% | $2-5 |
Fine free gold | CIL/CIP | 90-98% | $15-25 |
Refractory sulfides | Flotation + Oxid. | 85-93% | $30-45 |
Carbonaceous | RIP/CIL | 88-96% | $25-40 |
Critical factors we evaluate when designing separation circuits:
- Gold Particle Size
- +100 micron: Gravity first
- -100 micron: Direct leaching
- Sulfide Content
- 5% sulfides usually require flotation
- High arsenic needs specialized treatment
- Organic Matter
- Carbon absorbs gold – needs pretreatment
- We use ozone or chlorine oxidation
Metal Recycling and Environmental Systems
-Achieving a balance between economic efficiency and environmental compliance
1. Desorption electrolysis
- Desorption rate: >99.3% (high temperature and high pressure desorption tower)
- Electrolysis of gold sludge: purity 99.5%, silver synchronization recovery rate 82%.
2. Tailings treatment
- Dewatering index: water content of tailings ≤18% (high-frequency dewatering screen + filter press)
- Harmless treatment: CN <05mg/L (HJ 2025-1095 new emission standard)
- Resource utilization rate: Fe≥55%, S≥42% (mandatory recovery index in 2025)
Conclusion
Modern gold processing requires integrated systems from crushing to final recovery. Each stage affects the next, demanding careful optimization. Our experience shows that plants combining crushing optimization, precise grinding, and method-matched separation consistently achieve 92-97% recovery rates. The right equipment selection and process controls can transform marginal deposits into profitable operations while minimizing environmental impact.